to find out Gasket dispalcement & force
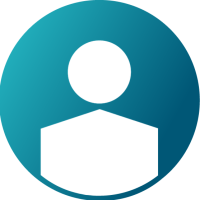

HI,
I am working on a rubber component.
objectoive: to findout the force required to get displacement of 1mm of rubber component.
steps followed till now: 1. used block 120 profile. 2. selected 'elastic>>m42_OGDEN. 3.
M42 law for rubber part & for steel plate M2 plas john law.Now analysis is running without any 'ERROR' but it is completed with 'no time'. Here rubber part is stationary & steel plate is moving.
problem:analaysis completed with below message
'NC= 0 T=0.0000E+00 DT=1.0000E+06 ERR=0.0% DM/M=0.0000E+00
ANIMATION FILE WRITTEN:TR4_0001 WRITTEN
RESTART FILES: TR4_0001_(0001_0001).rst WRITTEN'
Can any one suggest what is the coorect procedure to perform this analysis?
regards
Amlesh
Answers
-
Hi Amlesh,
Could you have make something wrong during the definition of boundary conditions like velocity etc..?
By the way,can you add the engine file that you used in the analysis ?
0 -
Hi Nskrtlus,
Thanks for quick reply. plz find below is Engine file text. No there is nothing wrong like velocity in assly. I used IMPDISP. I think analysis stop whenever there is contact between rubber & steel. As there large difference in between property of rubber & steel, software doesnot recognise it.
Engine file text:
/VERS/110
/RUN/r1/1/
3.0
/ANIM/VECT/DISP
/ANIM/VECT/FINT
/ANIM/VECT/PCONT
/ANIM/VECT/VEL
/ANIM/VECT/FEXT
/ANIM/VECT/CONT2
/ANIM/VECT/FOPT
/ANIM/ELEM/VONM
/ANIM/DT
0.000000000000000 0.100000000000000
/PRINT/-1000
/TFILE/1
0.100000000000000
0 -
Hello Amlesh,
I'm not sure about it because there are a lot of examples with rubber-steel connection in Radioss even i have done before but ,If you think it is about contact you can try Istf =4 (stiffness definition flag)
Maybe you can refer to example 42 to make comment about your problem; file:///C:/Program%20Files/Altair/12.0/help/hwsolvers/hwsolvers.htm?example_42___rubber_ring.htm
Regards.
0 -
Hello Nskrtlus,
Thanks for reply.
I am referring the same tutorial & using same engine file now. Only thing is that I have not used Istf=4. (i.e. example 42)
let me perform an iteration with it & check.
Meanwhile if possible could you please share an engine file for one of your rubber component project? i want to compare it with my engine file & understand the difference because now analysis is running without any error.so simulation model is ok only change in engine file.
Thanks in advance.
Regards,
0 -
Hi Amlesh,Here is my engine file sample./ANIM/DT0.000000 0.150000/ANIM/MASS/ANIM/NODA/DT/MON/FULL/PRINT/-10/RUN/ass2_mb3/1100.01/TFILE/4# dT_HIS0.001000/TITLEfinal/VERS/110/ANIM/VECT/VEL/ANIM/VECT/CONT/ANIM/VECT/FOPT/ANIM/ELEM/ENER/ANIM/ELEM/EPSP/ANIM/ELEM/HOURG/ANIM/ELEM/VONM/DT/NODA/CST/00.67 0.0001
0 -
Hello Nskrtlus,
Many thaks for your help!
yesterday I couldnot reply because of some technical problem.
Now the analysis is working. I will review it further & get back to you if required.
Once again thanks for your quick help.
/emoticons/default_smile.png' alt=':)' srcset='/emoticons/smile@2x.png 2x' width='20' height='20'>
regards,
Amlesh
0 -
Hello Nskrtlus,
I modeled as you suggested but now the bottom plate is interecting with rubber part. I used type 7.
I used to plates(steel) the top one is fixed with all DOF fixed.Bottom plate is movable in Y direction only. In between I placed rubber part.
why the plate is interesting the rubber part? could you please suggest the possible causes for the same?
Could you explain how did you calculated below from your engine file?
/DT/NODA/CST/0
0.67 0.0001Thanks in advance.
regards,
Amlesh
0 -
Hi Amlesh,
Can you tell which unit system do you consider?It is not define in the 'header card' . By looking the definition that you did in material properties,i think you used 'g-mm-ms-N' .But in that case,the rubber component seems like it have only 10 mm height ,is that true in reality?
Also it seems like there are some extra constraints in the model,because it gives 'incompitable kinematic condition' during solving.I think 'plateSPC,TOP_FIX and Impdisp_dof2' BCs are enough in your case.
Could you please check this issues?
Regards.
0 -
I also recommend you to define contact not separately,but selecting two component and activating 'create symmetric interface' in HyperCrash contact definition,so in one contact rubber will be 'slave' side and in the other contact it will be 'master' side.
0 -
Hello Nskrtlus,
Thanks for quick reply!
Yes. I am using 'g-mm-ms-N' unit. The height of the component is also 10mm. There are few projects in pipeline with bigger in size since this is my first project I choose the small one & then later bigger.
I will check analysis by removing all extra constraints & soon get back to you.
regards,
Amlesh
0