Composite size optimization doubts (ply thickness)
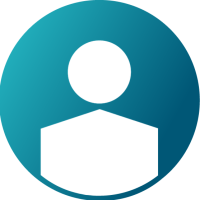

Hello,
I'm performing a composite optimization and I have some doubts about the thickness of the plies at different steps.
1) First while defining the different plies and generating the laminate, which thickness should I set to each ply? The real properties of my material has a thickness of 0.244 mm. Is that thickness the one I have to use in th definition of the plies? Or which value? Is a bit 'random' (normally in the tutorials is about 0.2mm) or where it comes from?
2) Later (after running the analysis and the free size optimization) for the discrete sizing, what does the TMANUF value means? Is that the real value of the ply thickness, so in my case 0.244 mm?
3) Also in the discrete sizing there is the option of setting un upper bound value for each size. I've already set the min. and max. thickness of the whole laminate, and all my plies are the same thickness. So does it make any sense to set a upper bound to each ply? And in function of what is set this value?
4) And the last question is about the initial number of plies when define the plies and create the laminate. My composite material is twill, so it just has 0º and 45º orientations, this means 2 different plies. When I create the laminate it doesn't allow me to repeat any ply, so if I create the 2 difeerent plies my laminate s going to have 2 plies, not more. But I want at least 4 or 5 plies. Cause if I just set 2 plies, the analysis results are bad (the displacement too high cause 2 plies is not enough for my model). So how I should I do? It is ok if I create 5 plies, the 1-3-5 are the same (orientation 0º,same thickness,same material) and the 2-4 are the same (orientation 45º,same thickness,same material)? Or is better for the solver if I define just the 2 different plies? What difference is going to make this in the final optimization results?
Thank you for your time and answer! /emoticons/default_smile.png' srcset='/emoticons/smile@2x.png 2x' title=':)' width='20' />
Answers
-
Ans2. MANUF defines the thickness of one manufacturable ply. This parameter is used during sizing optimization to automatically create discrete design variables such that the thickness of the ply bundle is equal to a multiple of TMANUF.
0 -
Altair Forum User said:
First while defining the different plies and generating the laminate, which thickness should I set to each ply? The real properties of my material has a thickness of 0.244 mm. Is that thickness the one I have to use in th definition of the plies? Or which value? Is a bit 'random' (normally in the tutorials is about 0.2mm) or where it comes from?
If you want to generate a concept for your design you can start with a rounded or near rounded thickness say like 0.3mm. Since 0.244 is the available ply thickness from the manufacturer you can use that during sizing which will be your TMANUF.
Altair Forum User said:Also in the discrete sizing there is the option of setting un upper bound value for each size. I've already set the min. and max. thickness of the whole laminate, and all my plies are the same thickness. So does it make any sense to set a upper bound to each ply? And in function of what is set this value?
I don't think it is not really necessary when you have a TMANUF.
Altair Forum User said:And the last question is about the initial number of plies when define the plies and create the laminate. My composite material is twill, so it just has 0º and 45º orientations, this means 2 different plies. When I create the laminate it doesn't allow me to repeat any ply, so if I create the 2 difeerent plies my laminate s going to have 2 plies, not more. But I want at least 4 or 5 plies. Cause if I just set 2 plies, the analysis results are bad (the displacement too high cause 2 plies is not enough for my model). So how I should I do? It is ok if I create 5 plies, the 1-3-5 are the same (orientation 0º,same thickness,same material) and the 2-4 are the same (orientation 45º,same thickness,same material)? Or is better for the solver if I define just the 2 different plies? What difference is going to make this in the final optimization results?
Slicing up of ply thickness completely depends on the your TMANUF (if provided). For instance your laminate thickness is 1 and your TMANUF is 0.5 then you will end up with 2 plies.
if you need more slices reduce the thickness of manufacturable thickness.
0