Pins fem analysis
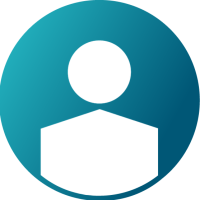

Hi everybody,
I am a mechanical engineering student and I’m doing a project for a skid steer loader. In particular I am studying the structural analysis of arm in the severe operative conditions. This analysis includes, in addition to the arm, bucket (where is apply the force) and two other bodies with which the arm is connected to the frame. To define the connection between the bodies I decided to make the hinges by contact with the pins. This contact has been achieved using the contact surface type slide. The analysis target is to determine the resistance of arm and pins.
Said this I would like to know I can optimize that analysis? Especially how can I improve the analysis on the pins?
Thanks in advance for the help.
Answers
-
Could you share some pictures to better understant your question?
0 -
Hi Q,Nguyen-Dai,
attached are some pictures of the model in analysis. In particular I have been shown better images depicting the pins discussed above.Thanks in advance for the help.
<?xml version="1.0" encoding="UTF-8"?>
<?xml version="1.0" encoding="UTF-8"?>
<?xml version="1.0" encoding="UTF-8"?>
0 -
As you do all with solid meshing, contact should be defined between ONE part and the pin. Another part will be 'tied' to the pin.
This method needs some attention about meshing technique: contact zones should be correctly splitted on all parts.
Why you make all in TET mesh? This structure is rather simple so it's better to work with HEX mesh, right?
0 -
Hi Nguyen-Dai.
My name is Stefano and I am working with Antonio to the skid loader project.
I will attach you some images about two diferrent analysis:<?xml version="1.0" encoding="UTF-8"?>
Left side: the analysis were conducted by considering slide contacts between the single parts and the pins
Right side: the analysis were conducted by considering contact between one part and the pin and the other part tied to the pin (as you suggest)
Now I will show you the Von Mises stresses on the pins, for each analysis:
<?xml version="1.0" encoding="UTF-8"?>
Like before on the left side there are results concerning the first analysis, on the right side the second one.
In fact it seems tha pins work better (less Von Mises stresses) in the second configuration.
However pins whose connect the lifter cylinder to the bucket are still too stressed. I don't know if I'am doing something wrong....
At last, I attach the last analysis that I ran in which I supposed all TIE interfaces:
0 -
I know nothing about BC & Loading of your analysis. So I can't say more about the results.
But in reality, you can not tie the pin to 2 parts. In general, we tie pin to one part (external) and make slide contact to another part (internal).
Numerically, you can make both slide contact to 2 parts, but you have to add some BC to pin to keep them out of rigid modes.
0 -
I try to explain better the purpose of this analysis.
I applied 6 constraints (12356 dofs) to the holes which serve for anchoring the arms and the cylinders to the loader frame. Then I applied a load (a pressure) to the bucket surface.
So I expected a symmetrical stress distribution. Furthermore my target was to study even the stress distribution on the pins which connect the different elements of lift arm.For this purpose I suddenly thought that I had to apply contacts between the pins and the other components. Now the problem is that the stress distribution on the arms and on the pins is quite different if I use contacts or ties.
I applied:
1st case: slide contacts for all surfaces;
2nd case: contacts for internal surfaces and ties for external
3th case: ties for all surfaces
By observing results it seems that the third analysis returns the most plausible results.....but it is should be wrong.
.
0 -
Hi @Stefano1988, @Q.Nguyen-Dai
I feel second approach is practical. One component has to move relative to other around an axis.
0