Solid Map - Hex Mesh
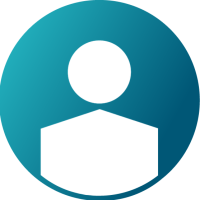

Hello,
I am meshing an assembly of many complex components with Hex elements in Ansys user profile. I wanted to know about how to get node to node connectivity ? What should be ideal value of Tolerance in edges/faces panel ? Please find the description of problem below.
In order to get best mesh quality, I splitted the complex solid component into different solids. Then, I meshed each divided simple solid with 2D mesh with keep connectivity on. Then, I went for solid map general and created hex mesh. but for different divided solids of the same component, I used different mesh size when i dragged them along length. And there is no node to node connectivity between different divided solids of the same component. How to resolve this?
The image shows divided solids of the same component with different mesh size.
Thank you for your time
Answers
-
Hi SamipJoshi,
You cannot get the connectivity if you mesh different solids separately. You should mesh one solid first and then use elements of this solid and map it to adjacent solid.
Please refer this tutorial, you'll understand properly.
https://altairuniversity.com/wp-content/uploads/2012/11/Tutorial_steeringwheel_hexa.pdf
Thank you
0 -
For an assembly, try to mesh with same density on 'contact' area and use 'equivalent nodes'.
0 -
0
-
Altair Forum User said:
Hi SamipJoshi,
You cannot get the connectivity if you mesh different solids separately. You should mesh one solid first and then use elements of this solid and map it to adjacent solid.
Please refer this tutorial, you'll understand properly.
https://altairuniversity.com/wp-content/uploads/2012/11/Tutorial_steeringwheel_hexa.pdf
Thank you
Thanks Premanand. But the main objective of meshing different splitted solids of the same component with different mesh size was to reduce overall number of elements and nodes. So wherever there is a contact, I need higher density of mesh but at no contact zone, i need coarse mesh so that I can reduce overall element count.
My length of the component is very high compared to width and thickness. So, with your approach I am getting too many elements and nodes.
0 -
While mapping increase the element size using below highlighted option, in the regions where you want coarse mesh. This will give you same mesh size but length of the elements will be increased. In this way you can keep the connectivity and also reduce some elements. Please try this and let me know if this works for you.
Thank you
0 -
Altair Forum User said:
Thanks Premanand. But the main objective of meshing different splitted solids of the same component with different mesh size was to reduce overall number of elements and nodes. So wherever there is a contact, I need higher density of mesh but at no contact zone, i need coarse mesh so that I can reduce overall element count.
If you would like to do different density meshes, and you would like to assembly them, you have to make a transitory zone for each changement of size.
0 -
Thanks Premanand and Nguyen-Dai.
Please find the attached images. This is a single component splitted into different solids. One is the cross section and one is isometric view. As said the length is too high than cross sectional dimensions. The area in the red region is where I want very fine hex mesh over the length. All the other area, I require coarse hex mesh.
Please suggest me a procedure to this.
Thank you for your time,<?xml version="1.0" encoding="UTF-8"?>
0 -
You should map it with 2 directions, layer by layer, similar to this t-weld:
Please upload cad model then we will give a try.
0 -
Thank you so much tinh. This is the kind of mesh I would like to generate. But, I am not sure if I can share my CAD geometry (Because of university research). so, would it be possible for you to share some initial steps on how to achieve solid map in 2 directions, layer by layer?
Thank you for your time,
Samip Joshi
0 -
You need two transitory zones:
0 -
-
Yes
/emoticons/default_tongue.png' srcset='/emoticons/tongue@2x.png 2x' title=':P' width='20' />
0 -
Hello,
What is the default element type that Hypermesh creates for the Hex Mesh Elements ? (I am using ANSYS user profile in HyperMesh)
How can I export this hex mesh generated in ANSYS user profile to the Ansys Workbench?
Thank you for your time,
Samip Joshi
0 -
You have a lot of choice of element types for ANSYS solver.
0 -
Altair Forum User said:
Hello,
What is the default element type that Hypermesh creates for the Hex Mesh Elements ? (I am using ANSYS user profile in HyperMesh)
How can I export this hex mesh generated in ANSYS user profile to the Ansys Workbench?
Thank you for your time,
Samip Joshi
I see default hex8 is SOLID45
so you need to assign ET solid45 to the hexa component
then export it
0 -
Thank you for the response.
I have vertical section and horizontal section meeting each other as shown in figure. I want to have node to node connectivity between these two. And also I will meshing horizontal and vertical sections with varying mesh density to get less number of elements. How to do this?
0 -
The unique method is one as described on above posts. Please proceed.
0 -
Error - More than one element type exists in component. when I open Tools > Component Table because I have hex20 and penta15 in the same component. How do I resolve this error and export my mesh from Ansys profile of Hypermesh to Ansys workbench?
0