Slide Contact between edge and solid face / Autocontact
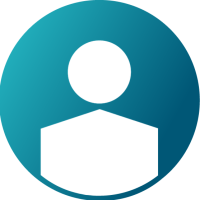

Hi,
am trying to create a perpendiculat contact between an edge of a 2D Midsurface mesh and one face of an solid.
I am proceeding the same way, like it would be a contact between to parallel faces, but somehow its not working.
Thank you for your help and have a good day!
Answers
-
Hi,
choose the nodes on the edge as slave and use node to surface contact (DISCRET=N2S). Note however the contact surfaces of solid frame will only engage one node (at the corner of shell) when displaced in positive z-direction, because the shell mesh is so coarse only one node overlaps contact surface.
Check the sample model with edge to surface contact.
0 -
Hi Ivan, thank you for your help. It is working now.
But I do not really understand the difference between the master and the slave. Why is it not working when I am using the edge as master?
0 -
Glad to hear it is working. It's not working when the master/slave are swapped because nodes lying on the master surface can freely penetrate on slave surface.
Interfaces are based on master / slave treatment. Contact can only occur between a set of slave nodes and a set of master segments. Master segments are defined depending on the type of element they lie on. If it is a 3-node or a 4-node shell, the segment is the surface of the element. If it is a solid element, the segment is defined as a face, Finally, if it is a 2D solid element (quad), the segment is a side.
Check the following documents:
http://blog.altair.co.kr/wp-content/uploads/2013/03/CONTACT_Card.pdf
0 -
Hi Ivan,
thank you very much. Very helpful!
0 -
I have a new problem now:
I have a lot of components for which I need to define several contacts. So I am trying to use the autocontact function.
Unfortunately not every contact is detected. How is the AutoContact working so I can optimize the parts that AutoContact is working properly?
I am using Shell thickness as Contact Tolerance type and the shell thickness is defined properly.
Most of the problems occure when tetra solids and midsurface meshes should be connected (See attached picture).
Thank you for your help.
Vincent
0 -
Maybe the contact was not detected because shell thickness is smaller than the gap between solid and shell midsurface.
Measure the gap (F4) and use Vicinity tolerance instead and provide a slightly increased gap.
If other unwanted contact pairs are then detected consider creating the problematic contacts manually.
0 -
Thank you Ivan, you helped me a lot.
0