Conductor Surface Thickness Setting Guidelines
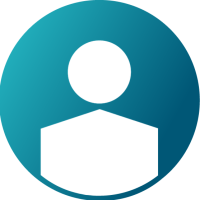

I just getting started with FEKO and I need to add some real conductors to my model. Using the default solver, I understand that I need to set the relevant volumes to free space and corresponding faces to the desired conductor. However, I am a little confused on how to go about the 'thickness' setting. If I am dealing with a thick conductor, my understanding is that I simply pick a value that is greater than skin depth for the metal and the simulation frequency. Is this correct?
Also, in several of my simulations, the thickness of the metal in the model is actually less than skin depth. In order to model these realistically, what thickness do I need to set for the face material? Should I use the actual thickness of the metal for both the top and bottom faces? Half the real thickness for the top and bottom faces? Or the full thickness for the top face and no material set for the bottom face?
Any insight would be greatly appreciated. Thanks!
Answers
-
Hello
You can refer to the 'SK Card' section of the User Manual for an in-depth explanation of skin depth and the thickness requirements.
See also the following forum post:
Here is an extract from that thread:If you model the platinum as a sheet with the appropriate thickness set on the face, the SEP solution should be very accurate since it will model a single current on the face with the correct resistance, taking the skin effect into account. This is the case for a very thin face, where the skin depth is much less than the thickness. On the other side of the spectrum (not your case), where the skin depth is much smaller than the region, the answer will also be accurate. Where you need to be careful, is when the skin depth is roughly the same as the thickness. In that case it is probably required to model the face as a finite thickness region (thus, faces on both sides). The reason for this is that the currents on the two sides are probably comparable, but you want to model them as two currents and not as a single current (an example could be that the current on the one face could be half that of the current on the other side). When modelling finite thickness sheets, a general rule of thumb is that your mesh elements should not be larger than the distance between the two faces. That means that the lower the thickness, the smaller the required mesh.
Note that the thickness is usually not modelled in a MoM simulation by creating a finite thickness region (unless the conductor is very thick and modelled as you described in the first part of your post), but rather as a face with the thickness applied to the face.0 -
Thank you for the reply MvdM. I know this topic is old, but I'm still struggling to understand how the conductor thickness setting works. As you mentioned, I am modelling a relatively thick conducting trace that is near the skin depth for the frequency simulated and am thus modeling it as a finite thickness region having a four-sided rectangular cross-section. In this case, would it be most appropriate to set the thickness of the top and bottom conductors as HALF the actual thickness of the trace or both the top and bottom conductors each as the ENTIRE thickness of the trace.
Your input would be greatly appreciated.
Thanks again!
0 -
Hi,
You should set the thickness on each face to be the actual physical thickness of the conductor (and not half on each). Feko will model an equivalent surface current modified to account for the physical thickness as specified.
Kind regards,
Johan H
0 -
That's what I was looking for. Thanks!
0