Query on meshing
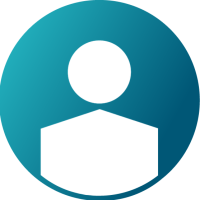

Dear all,
I have following doubts in meshing:
- What if I do good meshing in one portion of solid (say critical portion) and poor quality mesh in some other portion, do the results in the good mesh region are affected by the results of poor mesh region. Or do they remain unchanged? If possible, please explain the reason for the answer.
- What if we couldn't maintain uniform mesh size in non linear analysis?, If I use small elements to capture the geometry and large elements to keep nodes as less as possible then it causes sudden transition between the two. Does it affects the results badly or increases the solving time?
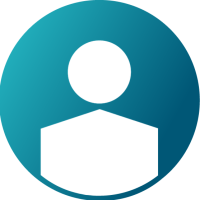

Hi Amar,
I think for 'good mesh' you are meaning a fine mesh. Fine mesh does not mean good mesh.The purpose of meshing is to get solutions in discrete locations. Good mesh is the mesh that serves your project objectives. So, as long as your results are accurate enough for your project, your mesh is sufficiently good. The most fundamental and accurate method for evaluating mesh quality is to refine the mesh until a critical result, such as the maximum stress in a specific location converges (i.e. it doesn’t change significantly with each refinement).
Normally if a mesh is too dense, it will require a large amount of computer memory and long run times, especially for nonlinear and transient analyses. In such cases the critical regions are meshed fine so that the results at those region are well captured. The user has to judge on this based on the model, analysis and experience.
Please go through Practical Aspects of Finite Element Simulation (A Study Guide) ebook which contains all practical concepts on FEA with examples.
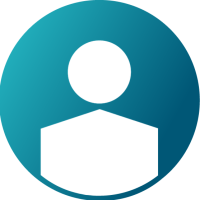

Hi Amar,
I think for 'good mesh' you are meaning a fine mesh. Fine mesh does not mean good mesh.The purpose of meshing is to get solutions in discrete locations. Good mesh is the mesh that serves your project objectives. So, as long as your results are accurate enough for your project, your mesh is sufficiently good. The most fundamental and accurate method for evaluating mesh quality is to refine the mesh until a critical result, such as the maximum stress in a specific location converges (i.e. it doesn’t change significantly with each refinement).
Normally if a mesh is too dense, it will require a large amount of computer memory and long run times, especially for nonlinear and transient analyses. In such cases the critical regions are meshed fine so that the results at those region are well captured. The user has to judge on this based on the model, analysis and experience.
Please go through Practical Aspects of Finite Element Simulation (A Study Guide) ebook which contains all practical concepts on FEA with examples.
Thank you sir for your reply! But I mean what I wrote. Also I have gone through the book you suggested but I was unable to get what I need to know. I am putting my question once again here -
1) Does the meshing in one portion of a single component affects the results in other portion of the same component?
2) Does the meshing in one component of an assembly affects the results in other components of the same assembly?
What do I want is to mesh critical portions with good mesh quality and remaining portions with the mesh having quality only good enough to capture the features of the component. Please give me guidance for the approach I am thinking of.
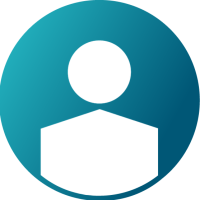

Hi Amar,
A low quality mesh lowers the accuracy of FEM results. Since we maintain continuity between components a poor mesh can affect other components also.
In general, poor element shapes can cause convergence issues in analyses and can produce inaccurate results.
You can NOT get 'good' results with 'poor' mesh, sure!
But you can make a 'fine' mesh within critical area for 'better' results.