2D Meshing issues
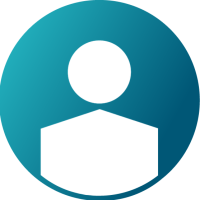
Hello everyone.
1. Is it normal that in HW CFD, the generated BL has non-uniform total height as shown in figure below?
2. I cannot generate tetra BL mesh even i change the BL element type from 'Hex or Prism' to 'tetra'. Can anyone confirm this?
Thanks in advance!
Best Answer
-
Nazrin_21804 said:
Thank you for the explanation and suggestion.
Changing the final height/base ratio does help. However, it gives very tall element for the last layer. Not sure how this tall element going to effect the results. However, I satisfy with your help, explanation and suggestions.
Btw, I would like to ask whether user can adjust the number of decimal point? Currently, all I can see is 2 decimal points. Is it possible to increase it up to 4? It give me uneasy feeling when I measured the cylinder, it shows 0.06m instead of 0.0554m.I wouldn't recommend leaving that base-to-height ratio at the large value - the default 0.8 is probably best. Just wanted to check if using the larger value gave closer to a constant column height, as it then becomes independent of the surface element size that may have some variation.
File > Preferences > HyperMesh Appearance > Drag the slider and look for Numeric Format -- set Precision to a larger value
1
Answers
-
How are you defining the meshing? Is this standard volume meshing - with Boundary Layers assigned to the surfaces? How are you defining the boundary layers first height - constant, fraction of surface size, etc?
0 -
acupro_21778 said:
How are you defining the meshing? Is this standard volume meshing - with Boundary Layers assigned to the surfaces? How are you defining the boundary layers first height - constant, fraction of surface size, etc?
hi acupro,
1. cylinder diameter: 0.0554m
2. edge > edge refinement size: 0.002
3. edge layer as shown in figure below:
4. volume:
addition:
I did play around with the setting. for example, i used all the 1st layer thickness definitions, growth rate, growth method etc. However, all changes give me uneven total BL height.
0 -
Nazrin_21804 said:
hi acupro,
1. cylinder diameter: 0.0554m
2. edge > edge refinement size: 0.002
3. edge layer as shown in figure below:
4. volume:
addition:
I did play around with the setting. for example, i used all the 1st layer thickness definitions, growth rate, growth method etc. However, all changes give me uneven total BL height.
I see. The boundary layers come from Edge parameters - then I assume you're extruding that. I have also noticed the edge boundary layers do not have the option to be created as tris instead of quads. The extruded elements from quads will be hex, and the extruded elements from tris will be prisms/wedges. Is there a reason you want/need tris as the edge boundary layers instead of quads?
For the equal boundary layer height, I would try constant first layer height, constant growth rate, and a large value (5 for example) for Final Layer Height/Base Ratio. Does that give you a more constant column height? Is there a reason for wanting/needing a constant column height?
1 -
acupro_21778 said:
I see. The boundary layers come from Edge parameters - then I assume you're extruding that. I have also noticed the edge boundary layers do not have the option to be created as tris instead of quads. The extruded elements from quads will be hex, and the extruded elements from tris will be prisms/wedges. Is there a reason you want/need tris as the edge boundary layers instead of quads?
For the equal boundary layer height, I would try constant first layer height, constant growth rate, and a large value (5 for example) for Final Layer Height/Base Ratio. Does that give you a more constant column height? Is there a reason for wanting/needing a constant column height?
Yes, i am extruding from the edge parameters.
Since i am ex-AcuConsole user, I was advised to use tetra element(s) instead of hexa. I believe this has changed?
For equal total BL height, I have no solid reason for it to be uniform. It just felt wrong when i saw the uneven total BL height (LOL). The uneven total BL height will become more worst when I meshed y+ < 1. For now, the y+ ~50.
However, I will try ur advised:"I would try constant first layer height, constant growth rate, and a large value (5 for example) for Final Layer Height/Base Ratio".
0 -
Nazrin_21804 said:
Yes, i am extruding from the edge parameters.
Since i am ex-AcuConsole user, I was advised to use tetra element(s) instead of hexa. I believe this has changed?
For equal total BL height, I have no solid reason for it to be uniform. It just felt wrong when i saw the uneven total BL height (LOL). The uneven total BL height will become more worst when I meshed y+ < 1. For now, the y+ ~50.
However, I will try ur advised:"I would try constant first layer height, constant growth rate, and a large value (5 for example) for Final Layer Height/Base Ratio".
The recommendation from the time of AcuConsole came from limitations with handling mixed topololgy/element-types on boundaries, where there was one boundary for the quads and another for the trias. This has been resolved some releases back, and is handled more efficiently writing the input files and meshes from HyperWorks CFD - so now there is no benefit to splitting elements back to tets.
I suggested trying the larger height-to-base ratio to see if a slightly different size in the surface mesh was leading to differences in how the final layers were sized, and the effect of the 'squeeze'. With the constant first layer height, and nothing limiting the growth of the layers, I would expect more uniform constant column thickness.
1 -
acupro_21778 said:
The recommendation from the time of AcuConsole came from limitations with handling mixed topololgy/element-types on boundaries, where there was one boundary for the quads and another for the trias. This has been resolved some releases back, and is handled more efficiently writing the input files and meshes from HyperWorks CFD - so now there is no benefit to splitting elements back to tets.
I suggested trying the larger height-to-base ratio to see if a slightly different size in the surface mesh was leading to differences in how the final layers were sized, and the effect of the 'squeeze'. With the constant first layer height, and nothing limiting the growth of the layers, I would expect more uniform constant column thickness.
Thank you for the explanation and suggestion.
Changing the final height/base ratio does help. However, it gives very tall element for the last layer. Not sure how this tall element going to effect the results. However, I satisfy with your help, explanation and suggestions.
Btw, I would like to ask whether user can adjust the number of decimal point? Currently, all I can see is 2 decimal points. Is it possible to increase it up to 4? It give me uneasy feeling when I measured the cylinder, it shows 0.06m instead of 0.0554m.0 -
Nazrin_21804 said:
Thank you for the explanation and suggestion.
Changing the final height/base ratio does help. However, it gives very tall element for the last layer. Not sure how this tall element going to effect the results. However, I satisfy with your help, explanation and suggestions.
Btw, I would like to ask whether user can adjust the number of decimal point? Currently, all I can see is 2 decimal points. Is it possible to increase it up to 4? It give me uneasy feeling when I measured the cylinder, it shows 0.06m instead of 0.0554m.I wouldn't recommend leaving that base-to-height ratio at the large value - the default 0.8 is probably best. Just wanted to check if using the larger value gave closer to a constant column height, as it then becomes independent of the surface element size that may have some variation.
File > Preferences > HyperMesh Appearance > Drag the slider and look for Numeric Format -- set Precision to a larger value
1