parts penetration issue in inspire motion analysis
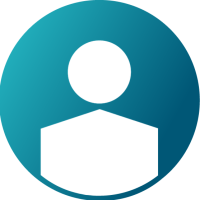
Hi
I am using the solid thinking inspire version 2020.0.1 for motion analysis. Currently i am working for the hinge motion analysis of our product. In model i am facing the parts penetration issue (Motion contact already given in the models)
Below are the reference image of model, yellow highlighted portion showing the penetration area.
Area where the parts penetrate each other showing high stresses in the part when analysis of parts done in motion simulation.
Collision type used motion contact: Poisson, Penalty: 100000N/mm coefficient of restitution:0.8, normal velocity: 0.001. Friction option enable.
Does anyone know how to resolve the parts penetration issue. Request you to please suggest the option
Answers
-
Hello,
Sorry for the late post...
Large penetrations at a contact interface could mean either 1) the stiffness is too soft for the problem at-hand, 2) there is something else in the model creating artificially high loads, or 3) the mesh used to represent the parts in contact is not accurately representing the geometry. It is difficult to say for certain from only an image.
Some suggestions:
- Make sure the model is not over constrained or there are redundant motions creating binding parts. Use the Force Explorer utility to view the force magnitude vectors for joints. Are the joints also seeing exceedingly high loads?
- Recommend using Impact method for the contacts. It is more consistent and robust and is the preferred (default) method. Damping can be adjusted fairly proportionally to adjustments in stiffness, but you should monitor by plotting "Penetration Velocity".
- Are these components steel? If so, try beginning with a contact stiffness (Impact method) of 1e4 N/mm, Solve and create a plot of the contact penetration depth. Is it exceedingly large? If so increase the stiffness slightly more and plot again, until you are seeing it converge to a more reasonable value (say .02 to .04mm, subjectively) . Note that you will never obtain a penetration of 0. You have to understand how contacts work to understand this (see the MotionSolve documentation). But also keep in mind that in the physical world there is always some level of compliance at surfaces in contact.
- If you are convinced the stiffness is sufficiently large (for example 5e5 N/mm) yet you are still getting large penetrations, you may need to focus on the resolution of the contact mesh. See the Inspire Motion HELP for more information on this. You can also take the .H3D file output from the Inspire Motion run (see run folder above Analyze Motion icon) and read it into HyperView and you can view the mesh used for the contacts.
Hope this helps get you on the right track.
Sincerely,
Scott Ziemba
Altair Engineering1