Shape Optimization Techniques for Designing Features - Part II
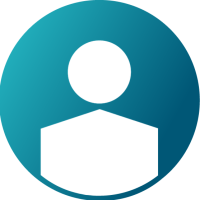
Product = GENESIS
This blog is the continuation of a previous blog entitled: “Shape Optimization Techniques for Designing Features - Part I”. In Part 1, we described how to create shape morphing boxes and shape morphing vectors that are used to define the shape optimization variables of a bracket. This blog will show the results of optimizing the location and diameter of a hole in the bracket.
Step 4: Set up the Optimization Problem
In this problem, we will minimize the strain energy of the structure while placing a geometric constraint to prevent the hole diameter to shrink less than 25 mm. The original diameter of the hole is 30 mm.
Step 5: Run the optimization with GENESIS and Compare Results
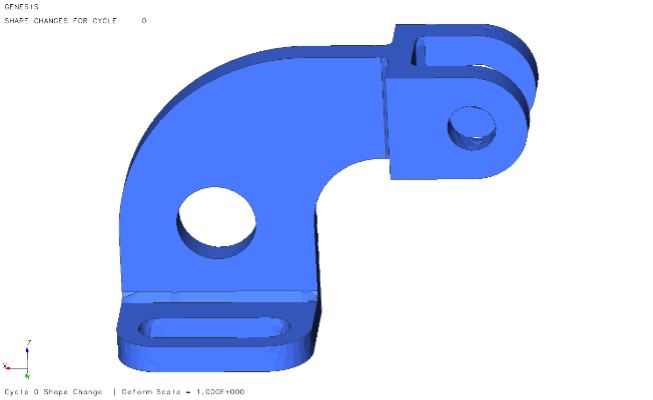
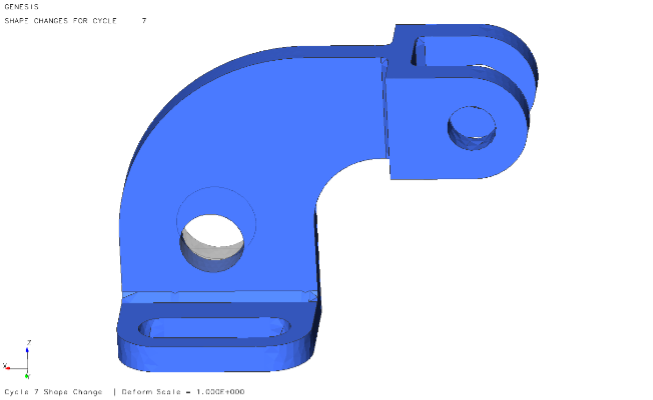
The optimization run took 7 design cycles to converge and at the end the objective was reduces by approximately 3% while the geometric constraint was satisfied.
Fig. 5.a shows the initial design, while Fig. 5.b shows the optimal design. The final shape revels that GENESIS moved all three design variables. It moved the hole down 8 mm and a about 2 mm to a side. It also reduced the diameter to its minimum allowable diameter.
The shape optimization process produced changes on both the displacements and stresses. Next, these results are shown.
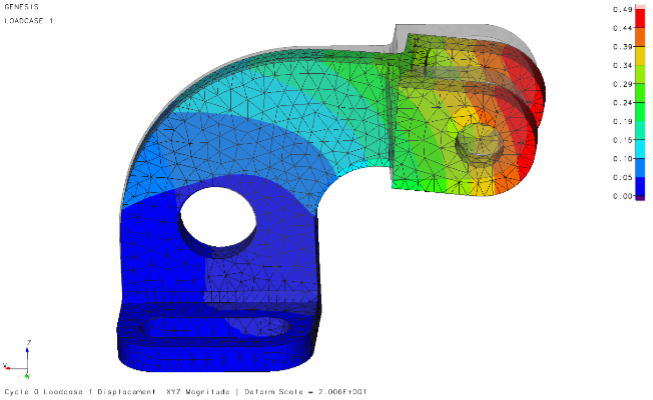
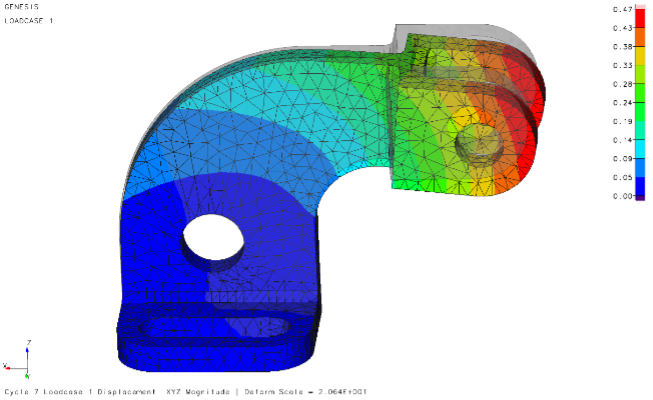
Fig. 6.a shows the displacements in the initial design, while Fig. 6.b shows the displacements in final and optimized design. The maximum deformation of the structure was reduced by about 4 %. This reduction is due to the objective function that was to reduce the strain energy to increase stiffness.
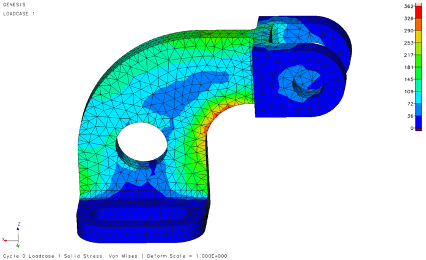
Figure 7.a
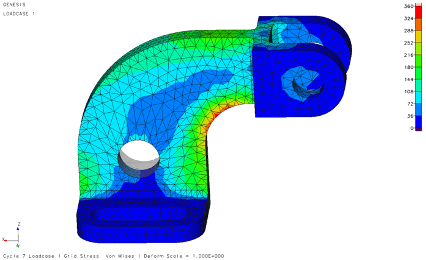
Figure 7.b
Fig. 6.a shows the stresses in the initial design. Fig. 6.b shows the stress in the final and optimized design. The stresses did not change significantly.
Conclusion: Designing features such as dimensions and location of holes is easy and effectively with the GENESIS software and its GUI Design Studio.