Combining Machine Learning and Simulation for Bulk Solids Mixing Optimisation
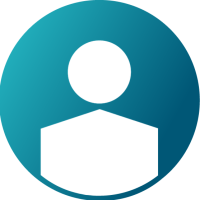
1. Introduction
All the requisite files for the case study can be downloaded here:
Continuous mixing is increasingly adopted in the bulk solids processing industries due to its higher efficiency relative to traditional batch mixing unit operations. However, the complex mechanics of continuous mixing is difficult to understand through measurement alone while physical trial-and-error process optimisation is time-consuming and expensive. This makes achieving reliability in continuous mixing processes difficult and problems like high wastage rates and process downtime persist, leading to economic losses.
Virtual optimisation that combines physics-based simulation with machine learning can be used to address these challenges by providing unprecedented insight into system mechanics and enabling the rapid and cost-effective optimisation of mixer design and operation.
This article details an efficient virtual optimization methodology that combines high-fidelity physics-based simulation in Altair EDEM, High Performance Computing (HPC) in Altair Unlimited and machine learning and automation in Altair HyperStudy to rapidly identify optimal mixer design and operation.
2. Methodology
2.1 Overview
An overview of the methodology is shown below and consists of parametrizing the equipment geometry, automatically generating and running Discrete Element Method (DEM) simulations for a well distributed quasi-random sample of the parameter space on the cloud and fitting a response surface to the results using machine learning. A genetic algorithm is then utilized to rapidly estimate the globally optimal parameter set from the fitted response surface. All of this is achieved via a highly automated, GUI-based workflow in Inspire, EDEM and HyperStudy.
2.2 Geometry Parameterization with Altair Inspire
The optimisation of the mixer design requires geometry parameterization which is performed in Altair Inspire. The design parameter space is defined by assigning variables to sketch and geometry tools and the Variable Manager within Inspire is used to update the values of the parameters to vary the design of the mixer. The parameter space for this case study is summarised in Figure 1 and is focused on the mixer shaft design.
| |
Figure 1 - Inspire Parameterization
2.3 Process Modelling and Parameterization with Altair EDEM
Altair EDEM simulations of the continuous mixing process are used to relate the design and operational parameters to process performance. An example EDEM simulation of the continuous mixing process is shown in Figure 2. The operational parameter space is defined directly in the EDEM model while the geometry of the mixer shaft for a given design configuration is generated in Inspire and imported into EDEM as a surface mesh. It is possible to vary a wide range of process parameters in EDEM including mass flow rates and equipment motions but in this case, the parameter space includes the rotational velocity of the mixer shaft only.
Figure 2 - EDEM Mixing Process Simulation
The process performance is measured in terms of mixture uniformity, energy consumption and throughput which are quantified by the particle residence time in the mixing chamber, mixer shaft torque and outlet mass flow rate in the EDEM simulations respectively. The equipment cost in terms of the number of paddles is also considered in the subsequent optimisation.
2.4 Automated DoE Generation with Altair HyperStudy
The virtual optimisation requires the generation of simulation results for a number of parameter combinations. This process is automated in HyperStudy using the EDEM-HyperStudy connector which enables the parameterization of EDEM simulation decks and the automatic generation and execution of simulation cases. The shaft geometry generation and import into EDEM is also automated in HyperStudy using a simple Python-based script that leverages the Inspire Applications Programming Interface to vary the shaft design parameters and trigger the geometry export. This enables HyperStudy to automatically vary both the process and design parameters in the EDEM simulations.
The HyperStudy Design of Experiments functionality is used to sample the parameter space in a way that is efficient for either statistical analysis or model fitting. In this case, the well-distributed sample of 37 cases shown in Table 1 was generated using Modified Extensible Lattice Sequence (MELS) sampling, which is efficient for response model fitting.
Table 1 - Portion of the MELS DOE
2.5 Simulation Processing with Altair Unlimited
The Discrete Element Method that powers EDEM is the highest fidelity numerical method for simulating the behaviour or bulk solids available today, but it can be computationally expensive and high-end graphics cards may be required to achieve practical solve times. Altair Unlimited provides a turn-key HPC solution to overcome this challenge by offering powerful hardware and efficient job management in both on-premises and cloud-based formats.
EDEM jobs can be submitted from a local HyperStudy instance directly to a remote Altair Unlimited HPC node via the EDEM-HyperStudy connector as illustrated in Figure 3. This eliminates the need for manual file transfer or job submission. Users can specify which files to download back into their local machine after processing, which to keep on the cluster and which to discard thereby reducing data storage and transfer requirements. In this case study, only tabular data of the mixer Key Perfomance Indicators (KPIs) was extracted back to the local machine and collated in HyperStudy.
Figure 3 - Altair Unlimited Submission via EDEM-HyperStudy Connector
2.6 Statistical Analysis, Machine Learning and Optimisation with Altair HyperStudy
Once the simulation data is available it is useful to perform statistical analysis in order to understand the parameter sensitivity. This can be achieved directly in HyperStudy and a wide range of analysis tools are available. In this case, the Pareto plots shown in Figure 4 are a useful way to examine the parameter sensitivity.
![]() | ![]() |
Figure 4 - Pareto Plots for Residence Time and Total Mass Flow
A response model can also be fitted to the simulation data in HyperStudy using machine learning. The model predicts the values of the KPIs based on the variable parameters, eliminating the need for running additional simulations and thereby saving significant time and computational resources. A wide range of classical regression models are available in HyperStudy and a Fit Automatically Selected by Training (FAST) method is available to automatically determine the most accurate model based on generalised metrics.
In this work, the FAST method was used to fit models for the mixer KPIs and their residual analysis is shown in Figure 5.
![]() | ![]() |
Figure 5 - HyperStudy Residual Plots for Residence Time and Total Mass Flow
The fitted response models can be used for the rapid optimisation of the mixer design and operation. This is achieved by operating on the fitted models using a Multi-Objective Genetic Algorithm (MOGA) in HyperStudy to efficiently identify the optimal parameter combinations for a given set of objectives. HyperStudy can evaluate thousands of different parameter combinations in seconds to find optima, and due to the competing nature of the objectives, trade-off curves in the form of Pareto fronts are obtained as shown in Figure 6.
![]() | ![]() | ![]() |
Figure 6 - Pareto Fronts for the Mixer KPIs
Alternatively, a weighted sum approach can be applied to converge to a single optimum based. This involves assigning weights to each objective that determine their relative importance. An example of a mixing performance optimal solution, which was obtained by assigning higher relative weight to the particle residence time, is compared to the baseline case in Figure 7 and shows improved mixing performance with similar shaft torque.
Figure 7 - Baseline and Performance Mixer Comparison
3. Conclusion
The Altair portfolio offers a comprehensive solution for the virtual optimization of bulk solids handling processes including CAD geometry parametrization with Altair Inspire, high-fidelity simulation with Altair EDEM, turn-key HPC with Altair Unlimited, and machine learning and optimization with Altair HyperStudy. Combining these tools enables the rapid and cost-effective optimisation of bulk solids handling processes in-silico.
For further information please see our webinar: Optimizing a Continuous Mixing Process with Discrete Element Modelling and Machine Learning
For a detailed description of the workflow please see our how-to video series: How to Optimize a Continuous Powder Mixer with Altair tools
Learn how to model the mixer drivetrain in this article: Modelling a Bulk Solids Mixer Drivetrain with EDEM, MotionSolve, PSIM and Activate
Are the python and batch files available for converting the inspire model to an stl?