Surface Hardening for 3d models
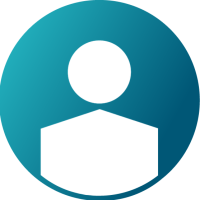
Hello Everyone ,
i want to know that how do I define surface hardening on 3d models.
I have a rubber component which has a hardened rubber on outside and softer one in the inside.
Also I would like to know this method for metals also. (Surface hardened)
Regards,
Bharat
- 3D mesh inside
- 2D mesh (membrane) covers 3D and share the same nodes as 3D
- 3D mesh inside
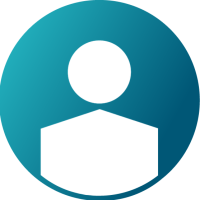
Hello Rahul,
This is required for all types of analysis.(non linear static,transient,fatigue, random). material is Rubber. But I would like to know it for metals also.
Thanks and regards,
Bharat
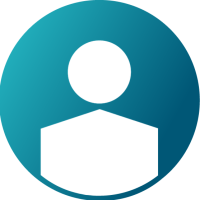

Hi Bharat,
In your model you have harder rubber on outside and soft material inside.
In this case you can have two components the outer with harder material and the inner with soft material.
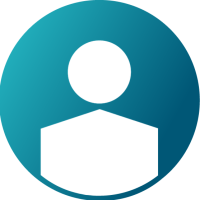
Hello prakash,
Thanks for the reply.
My hardened surface is very thin as compared to softer part. So,Isn't it possible that creating small elements on the harder part will give me unrealistic results?
Regards,
Bharat
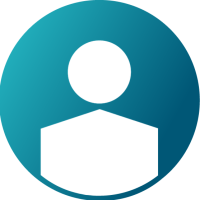

Hello prakash,
Thanks for the reply.
My hardened surface is very thin as compared to softer part. So,Isn't it possible that creating small elements on the harder part will give me unrealistic results?
What you need is a Finite Elements soft for 'microscopic' scale. I don't think you could do such simulation with 'normal' FE softwares, like Altair's solver, Ansys, MSC Nastran, Abaqus,...
Just my personal thoughts. Maybe not correct /emoticons/default_smile.png' alt=':)' srcset='/emoticons/smile@2x.png 2x' width='20' height='20'>
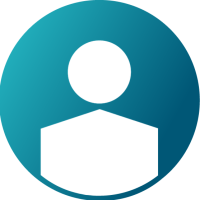
What you need is a Finite Elements soft for 'microscopic' scale. I don't think you could do such simulation with 'normal' FE softwares, like Altair's solver, Ansys, MSC Nastran, Abaqus,...
Just my personal thoughts. Maybe not correct
/emoticons/default_smile.png' alt=':)' srcset='/emoticons/smile@2x.png 2x' width='20' height='20'>
Hello Q. Nguyen-Dai,
Thanks for sharing your thoughts. Can you give any suggestions for my problem?
Regards,
Bharat
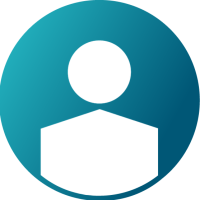

Maybe you can try :
I used sometime this technique (but the same material) to catch membrane stresses of 3D part analysis. My membrane has thickness about 0.0001 mm comparing to my part dimension 100~200mm.
I have no idea how this technique could help you.
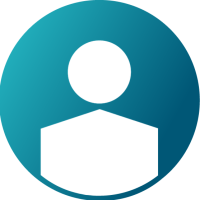
Maybe you can try :
2D mesh (membrane) covers 3D and share the same nodes as 3D
I used sometime this technique (but the same material) to catch membrane stresses of 3D part analysis. My membrane has thickness about 0.0001 mm comparing to my part dimension 100~200mm.
I have no idea how this technique could help you.
hello,Q. Nguyen-Dai
Thanks for bringing this point to me. I have never used joining 3d elements to 2d elements. Can you tell me how to do this?
Regards,
Bharat
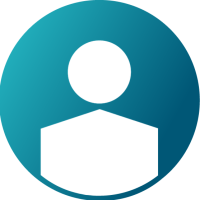

Make your 3D mesh. When finished, create 2D face by using 'Tool' => 'faces'. So you got 2D elements at 3D border.
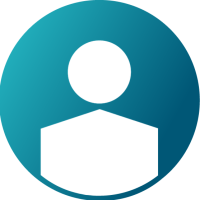
Make your 3D mesh. When finished, create 2D face by using 'Tool' => 'faces'. So you got 2D elements at 3D border.
Hello Q Nguyen-Dai,
Thank you for the reply,
Ok. But I was asking about connecting 3d elements to 2d elements (which are not made from surface of 3d elements). Can I connect them as both elements have different DOF per node? (2d having 6 and 3d having 3)
Regards,
Bharat
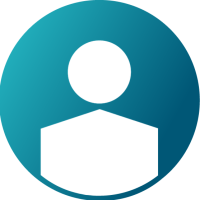

Bharat,
The face elements with the 3D elements will have a nodal connectivity.
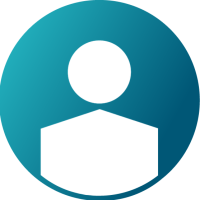
Bharat,
The face elements with the 3D elements will have a nodal connectivity.
Hello Prakash,
I am not quite sure that I understand what you are saying.
let me give an example.
I have a wall which I make with 3d elements and a cantilever beam in that wall (made up of 2d elements). How do I connect them?
Regards,
Bharat
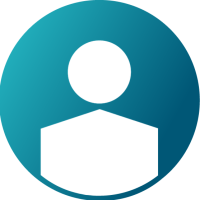

Hello Prakash,
I am not quite sure that I understand what you are saying.
let me give an example.
I have a wall which I make with 3d elements and a cantilever beam in that wall (made up of 2d elements). How do I connect them?
A Hypermesh model to show us your question ?
Bharat,
Yes, you can connect them,
Sandwiching: Having 1 or 2 layer of shell elements inserted between the solid elements at their junction. an extra layer of shell should be created inside/between the solids, helps create a smooth transition b/w solids and shells.
Using RBE2 to connect the shell and Solid elements. The independent should hold the Shell node and at least two dependent should hold the nodes on the Solid. Make sure you have nodes on Solid elements exactly of the PSHELL thickness.
Create skin of the solid elements and then connect the nodes of those skin elements with other shell elements.
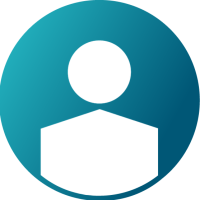
A Hypermesh model to show us your question ?
Hello Q. NGUYEN- DAI
I tried to upload the .hm file but it says that you are not allowed to upload this kind of file.So I have uploaded an image file for you.
Thamks and regards.
Bharat,
Yes, you can connect them,
Sandwiching: Having 1 or 2 layer of shell elements inserted between the solid elements at their junction. an extra layer of shell should be created inside/between the solids, helps create a smooth transition b/w solids and shells.
Using RBE2 to connect the shell and Solid elements. The independent should hold the Shell node and at least two dependent should hold the nodes on the Solid. Make sure you have nodes on Solid elements exactly of the PSHELL thickness.
Create skin of the solid elements and then connect the nodes of those skin elements with other shell elements.
Hello Rahul,
First method method is very much helpful but by my perception I find that this method can't be used to define surface hardening.(or any general case where your 2d elements form an envelope over 3d elements. e.g. surface hardening of a solid block).
this is my notion but I might be wrong. Can you please elaborate further on this?
Thanks and Regards,
Bharat
Hi,
Is this requirement for Fatigue or Nonlinear analysis?
Regards
Rahul R