Hexamesh-pump impeller
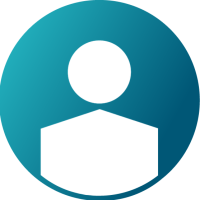

Hi everybody.
I'm new to Hypermesh and I have to do a CFD analysis of submersible pump impeller for a University exam. I started to realize the solid mesh of the impeller, but I encountered some problems.
My idea was to trim the impeller geometry in more solid parts; so I realized the 2d-quad-mesh and then by solidmap I tried to get the 3d-hexa-mesh.
First I'd like to understand if this is the best way to realize the hexa-mesh.
At this point I tried to merge the volume meshes, but the result was bad.
I attach the file .step of the impeller and the file .hm of the partial work I realized (in this file there is only one volume mesh!).
I hope you will help me!!
Best regards
Stefano
Answers
-
Hi Stefano1988,
It looks a bit complicated to hex mesh the propeller component. Since the ribs are curved and does not follow a pattern on both upper and lower side, I feel manually meshing will give good results.
Why not Tetra instead of Hexa?
0 -
Hi Prakash
Thank you very much for the quick reply.This is an exam project and the professor asked to create an hexa-mesh. I also thought that a hexa mesh is more appropriate for CFD analysis.
However I will present this problem to the professor.
Best regards
Stefano
0 -
Tetra elements can give you good results also, not only hexa.
Ask again your prof how he can do hexa mesh?
0 -
Hi everybody.
Suppose I can do a tetra mesh, what is the best way to do that? I think I must first trim the impeller in order to simplify the solid and divide it in more components; then I can do 2D mesh of the surfaces that I need. Finally I can do the 3D mesh by solid map or maybe I can use CFD tetramesh.
The problem is that I can't separate the blades from the rest of the body, since they are curved.
I attach again the .hm file, where I simply trim the impeller and where I tried to trim a blade.
Best regards
Stefano
0 -
You can work with surfaces instead of solids.
Yeah, to get good mesh, have to work, even work hard some time
/emoticons/default_smile.png' srcset='/emoticons/smile@2x.png 2x' title=':)' width='20' />
0 -
I'm working hard to try to get a good mesh, but unfortunately I can't get satisfactory result. This is the first time that I try to mesh a component and although I achieved the Hypermesh online certification, I can't get what I want. But I have to do it, so I keep trying!
I admit that I still tried to get an hexa mesh, but in the end I gave up, because I have a deadline to next Monday.
So I spent this afternoon trying to get a tetra mesh, by automeshing the surfaces and then using CFD tetramesh. Even if the 2d mesh quality index is not bad, when I run ' 3d check elem', 3d mesh presents a lot of errors.
I'm still working on solids; in particular I divided the impeller in three components: an upper base, a lower base and the group with the blades. I don't know if this is the right way. I hope someone can help me again.
Best regards
0 -
Altair Forum User said:
3d check elem', 3d mesh presents a lot of errors.
Stefano,
Can you post the error messages?
Is it something to do with tet collapse?
If it has to do with tet collapse, you can set the collapse quality in Tetramesh parameters as shown in the image
0 -
Hi Prakash.
Thank you for the reply.
Now I have a different problem. I made a 2d mesh of all surfaces, by dividing the model into sub components.
When I tried to do the CFD tetra-mesh, Hypermesh returned an error: 'Possible boundary self intersection found'. I'm pretty sure that the mesh is connected so I don't know what's wrong.
I attach the last .hm file. I hope you will help me.
Best Regards
0 -
Problem solved.
There were free element edges.
Could you please check tetra-mesh quality? Might it be appropriate for a CFD analisys?
I attach the .hm file.
Best Regards
0 -
I see you have only second order tetrahedral element in your model.You can refer Altair University Free FEA book for checking tetrahedral mesh quality.PFA screenshot for same.
Mesh quality is different for different type of analysis.(tet collapse & jacobian is important for structural analysis)
0 -
Hi Rahul.
Thank you for the reply.
I saw that there are elements that fail 3d-check, in particular tet-colllapse and jacobian. So I could correct these elements. I want to ask you: is better to correct the elements or maybe can I improve 3d-mesh quality by modifying the surface mesh? Maybe could I work with both tetra and hexa elements, by using hexa in areas with symmetries and tetra on the blades?
In the end I think the only way to check if the mesh is appropriate for CFD analisys is to try to do the analisys.
Best Regards
0 -
For Structural analysis....For complex geometry tet collapse should be greater than .1 & jacobian should be greater than .4.
You can improve element quality with remesh & manual method.But these days you canrun solver with poor quality elements.So please give a try.
0 -
This is a great thing!!!
I tried to autoremesh the elements and it led a decrease of errors number.
Just another thing: how can I export the mesh to Acuconsole? I am not able to do it.
If I can't use Acusolve, may I export the mesh to Fluent? I'm using Hyperworks student edition..
0 -
For importing the nas file in Acuconsole, kindly make sure that in HM:
· There are no free edges.
· No duplicate elements
· No intersection
· It should be a closed volume
0 -
Altair Forum User said:
Just another thing: how can I export the mesh to Acuconsole? I am not able to do it.
Hi,
Make sure you are in CFD AcuSolve profile and make sure there are no free edges etc... as @Rahul R posted in his previous post.
Go to File>> Export>> CFD>> AcuSolve, provide path to your working directory and click Export.
0 -
Thank you guys, your replies are very precious to me.
However I can't reach a conclusion. I try to explain my doubts.
I attach step file of my components. I have to do a CFD analysis on a pump stage. I'd like to know, from an inlet pressure, the outlet pressure at the end of the stage.
1- What do I mesh? Do I mesh the fluid flow or do I mesh the walls, the inlets and outlets?.
2- To mesh the fluid, may I use 'wind tunnel'?
3- Have I to use boundary layer mesh?
I'm sorry but this is the first time I do a CFD anlaysis, and sometimes I have no idea about what I have to do. I just need some advices to start meshing.
thanks
Best regards
0 -
-
Hi Ravi
Thank you very much for the reply.
I suppose that the mesh I see in the picture is the surface mesh; then I can do CFD tetramesh to obtain the volume mesh. Isn't it right?
Well that is a great suggestion.
Thank you again.
Best regards
0 -
Stefano,
yes you are right. the mesh in the picture is 2D surface mesh, use CFD tetra mesh to create volume mesh.
there are some fillets are spoiled, do correct it otherwise difficult to get good results.
Regards
Ravi
0 -
Thanks Ravi
Of course I will correct these elements at first.
Well, I will try an attempt today.
Have a nice day.
Regards
0 -
Hi Ravi
No way! I can't export the volume mesh in Acusolve becouse there were always free edges. I don't know what's wrong.
I created two surfaces: inlet and outlet. After creating these, I always equivalenced the surfaces. Then I created the surface mesh of all surfaces (include the fluid one).
After checking that there were not free edges I created the volume mesh. The volume mesh still presented free edges!
Furthermore how can I insert inflow and outflow surfaces mesh into the volume mesh? Aren't there problems with duplicate elements?
I attach my last attempt (where I don't care about mesh quality).
P.S. I think that I need to mesh even the wall. I have to do a CFD analysis of the entire pump stage. So I have a part of the fluid (the one in the impeller) that it is in rotation and the rest of fluid flow cross the diffuser. But now it doesn't matter! At first I'd like to solve the first problem.Thanks
Regards
0 -
Hi everybody.
I'm focusing on the impeller. At first I'd like to do a simple cfd analysis on this component. So I finally exported the mesh in Acuconsole. But now I have a question.
How can I impose a angular velocity to the fluid which crosses the blades? By meshing I obtained just one fluid volume; but the fluid before the inlet should not be in rotation.
I attach the .hm file.
Thanks in advance.
Best Regards
0 -
Hi everybody.
I made some attempts on Acuconsole but I obtained wrong numerical results.
The steps I followed were as follow:
- Flow Model: STEADY STATE - THREE DIMENSIONAL - TURBOLENCE (spalart allmaras)
- Incompressible fluid
- thermophysical properties costant
Essentially, sarting from impeller angular velocity and inlet pressure, I'd like to obtain pressure and velocity distributions.
At first I defined the angular velocity in 'Reference Frame' (I assigned rotation center and angular velocity (about 2500 rpm)).
In Acuconsole I assigned the following values:
- As volume I assigned the fluid volume (material:Water, Body Force:None, Reference Frame: angular velocity.
- For the surfaces, after assigning 'simple BC type' for each surface, I assigned:
- Pressure (about 400000 N/m^2) for inlet; a value of eddy viscosity;
- No BC for outflow (I'd like to obtain the outlet pressure!);
- Angular Velocity for wall;
- No BC for wall_2.
Even if the anlysis converges (after several time steps), and even if the velocity distribution seems to be reasonable, the numerical results are completely wrong.
Since I couldn't find neither tutorials, nor videos, nor any other material, my last chance was to ask for your help. I also made the blower workshop with which I was able to understand some issues about Acuconsole.
At last I attach the .hm file and the .acs files.
I really hope you can help me. At least tell me if I'm completely wrong.
Please answer.
Best Regards
Stefano
0 -
Created seperate topic in Acusolve. PFB link.
0 -
Ok thanks Rahul.
0 -
PFB reply in below post and continue it from there.
http://forum.altairhyperworks.com/index.php?/topic/19124-acusolve-query/
0 -
0