Flexible Body Assign Problems
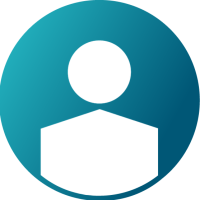
Hi everyone,
I'm modeling a full vehicle event and facing some problems when I try to alter the Rigid body by the Flexible body. With rigid body, my model run well. The error come when I chage body to flexible, the run no longer converge. I recognise It happen because the joint that fix the gear housing of steering boost to the flexible body. When I try to fix it to Chassis (Chassis is Rigid body and was fixed to flexible body) It still run. Could anyone please explain for me why It happen like that and what are comon mistakes leading to disconvergence of model? Below is the log file.
Thanks for your reading and I'm sorry if it is an inscrutable expression.
Time=1.119E-01; Order=2; H=8.365E-06 [Max Phi=8.134E-11]
Time=1.121E-01; Order=2; H=1.133E-05 [Max Phi=5.074E-09]
Time=1.122E-01; Order=3; H=2.474E-06 [Max Phi=1.879E-09]
Time=1.123E-01; Order=3; H=2.984E-06 [Max Phi=8.737E-11]
Time=1.123E-01; Order=3; H=5.273E-07 [Max Phi=2.332E-05]
WARNING: [DASPK] The nonlinear system solver in the time integration could not converge
.....
Time=1.123E-01; Order=1; H=2.153E-08 [Max Phi=6.221E-05]
Time=1.123E-01; Order=1; H=2.629E-12 [Max Phi=8.321E-05]
WARNING: [DASPK] The nonlinear system solver in the time integration could not converge
.....
Time=1.123E-01; Order=1; H=2.588E-14 [Max Phi=8.669E-05]
WARNING: [DASPK] The nonlinear system solver in the time integration could not converge
.....
WARNING: [DASPK] The nonlinear system solver in the time integration could not converge
.....
DAE SOLVER STATISTICS (DASPK-Index1)
------------------------------------------------
Number of solution steps = 556
Number of residue evaluations = 1701
Number of jacobian computations = 901
Number of error test failures = 7
Number of nonlinear convergence failures = 86
WARNING: Repeated abnormal return from integrator!
ERROR: At time=1.123E-01 the integrator failed to proceed.
Answers
-
Hi,
did you review the model in HyperView?
I recommending to set up a small print interval and run the model. And then review h3d file in HyperView. You don't need to run a long simulation, only few frames in results file can help you to find a mistake
I think this is the easiest way how to debug the model.
Pavol
0 -
Hi Pavol,
As you can see in log file, the simulation run several integrations before it doesnt converge. I cant recognise any problem with them, it's too short. Does the large deformation of flex body has influence to the convergent condition? I can see the big force in that joint when I perform simulation with rigid body.
Thanks.
0 -
If there is a big force in the joint with a rigid body, then it is likely your forces are unrealistically high. When you start to use the flexbody, this results in undesired behavior. This is a common issue. The forces are unrealistic, due to some problem with the model, but it runs because the bodies are all rigid, and therefore infinitely strong. When you start to use the flexbody, it deforms a large amount due to the extremely high forces.
It's also possible that your flexbody has incorrect property data, or you used incorrect units when creating it with flexprep. Look at the mass of the flexbody (in the bodies panel). Does the mass make sense? I would animate just the flexbody by itself, using HyperGraph. You can use this method to animate the mode shapes. Note: the first 6 modes in the file are rigid body modes, and can be ignored. But look at the first few modes. Is the frequency reasonable? When you animate the rest of the modes, do you see any parts that are not correctly correctly. Sometimes users will miss a connection here and there, which results in brackets not being completely attached to the rest of the structure.
In summary, this should be a two step process for you:
Step 1. Ensure the forces in the model are reasonable before adding the flexbody
Step 2. Ensure the flexbody is reasonable.
0 -
Hi Chris,
Thanks for your respond. Seems like my joints doent have the resonable stiffness. I'll try to find out that. When I run somes events link DouplaneChange, it usually has problem with my model. It can't take turn. The issue like this:
ERRMES:USER [386001]
<< ALTAIR DRIVER :: Steering Controller : Computed predicted path error > allowed path error of 1 mm.
Proceeding with the best approximation.
Possible Reasons:
1. Vehicle has spun out.
2. Path is not smooth
3. Steering wheel angle has reached saturation
.ERRMES:USER [386001]
<< ALTAIR DRIVER :: Steering Controller : Computed predicted path error > allowed path error of 1 mm.
Proceeding with the best approximation.ERRMES:USER [386001]
<< ALTAIR DRIVER :: Steering Controller : Computed predicted path error > allowed path error of 1 mm.
Proceeding with the best approximation.I really dont know why It happen and what can I adjust in my model. Could you give me some recommendation ?
Thanks.
0 -
Based on the limited information provided, we really can't offer much in terms of help. The possible problems are to many to discuss here.
Rather than start with a full vehicle model, you should be just the front and rear suspension separately. Using this method, you can use the half-car events to fully debug your model before going to complex full vehicle simulation.
When we assemble the full vehicle model, we first run simple events, like straight line acceleration and straight line braking.
If the model looks good with these events, then we run events like constant radius, and swept steer.
Only when the model is fully debugged, do we look at running events like lane change.
0 -
Hi,
i am also getting same issue, please find attached .log and flex.out files.
tried with different integrator tolerance but getting same error.
Thanks.
0 -
mpv-
When you attach the steering gear to the frame, are you using a single fixed joint? If so, this could be the cause of your issue. The forces (and especially moments) will not be physically realistic, and as a result, likely causing the integrator failures. In this kind of situation, we create interface nodes in the flexbody at each one of the bolt locations for the steering gear. So, you may need 3 more interface nodes, and then of course a bushing (or joint) to tie the model to the flexbody.
Chris
0