Topology Optimization for Additive Manufacturing
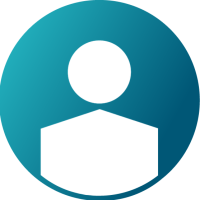
Product = GENESIS
Additive Manufacturing (AM) is a relatively new manufacturing process that can be used to generate complex parts which sometimes conventional processes cannot create. Topology optimization results can often be realized using AM. However, results from optimization cannot always be successfully or easily printed because topology might generate shapes that are not printable. Examples of structures that cannot be printed are the ones that have shallow overhang members.
In this blog, we will show that GENESIS can design structures for AM capable to overcome shallow overhangs. But before showing what GENESIS can do, let’s answer the following questions; 1) What is additive manufacturing? and 2) What is the critical overhang angle?
What is Additive Manufacturing?
Additive Manufacturing is also known as 3D printing is a manufacturing process in which a structure or a part is built with a 3D printing machine in a layer-by-layer fashion. In contrast to other fabrication methods, such as casting or forging, AM has the unique ability to generate complex parts without the need for expensive molds, presses, and/or tooling. On the other hand, in contrast to milling, AM does not waste too much material. AM has experienced rapid growth since the 1980s when important work and first patents were granted. This type of manufacturing technique was first conceived and used to generate prototypes and today is beginning to be used to create final products. The market for AM machines is growing rapidly and the fact that many of the initial patents have expired is allowing new companies to enter the market and reduce the cost of the 3D printers, as well as the material used to print.
What is a critical overhang angle?
Overhangs are design features that raise at an angle that deviates from the build direction. Overhangs which are below a certain critical overhang angle value are undesirable because they may be unstable and might require non-structural supports. These non-structural supports are typically costly, as they require extra material and extra post-processing of the 3D printed parts that contain them. The overhang angles are normally measured from the build plate. The value of the critical overhang angle depends on many factors, among them the 3D process itself and the material used. For example, for the fused filament fabrication (FFF) process a typical value of the critical overhang angle is 45o.
Topology Optimization Problem
To demonstrate topology optimization with overhang angle constraints, we will solve the following problem: Minimize the strain energy of the system subject to a mass fraction constraint of 30%. This will generate the stiffest structure possible reducing 70% of the material.
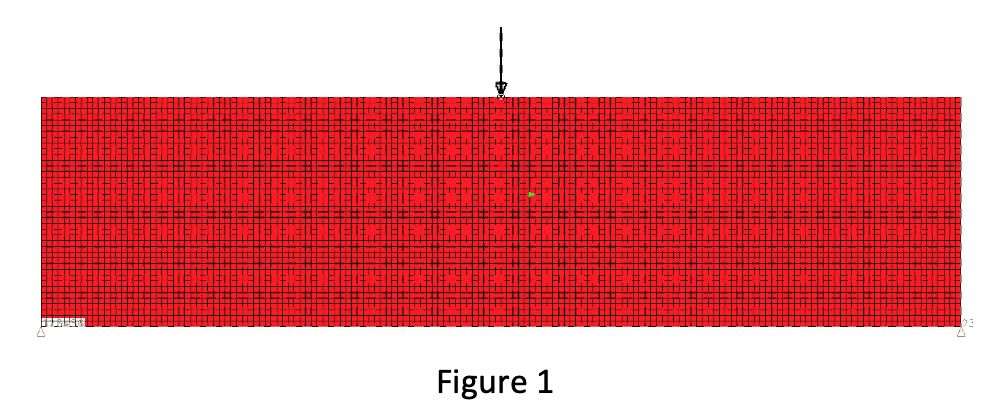
Standard Topology Results
Figure 2 shows the final topology optimization results. The generated structure makes sense as it can carry the load from the applied point at the top center of the design domain to the two support points in the bottom corners.
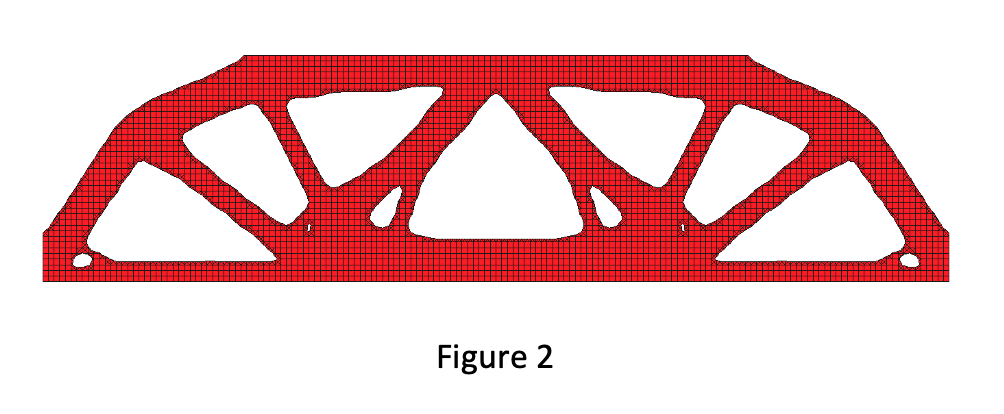
This answer, however, cannot be printed layer by layer vertically (using a printer that uses the FFF process) as it has several shallow members. Note that the top members are mostly horizontal.
Topology Optimization with Overhang Angles Constraint Set Up
To avoid overhang angles, in the GENESIS GUI (Design Studio), we only need to select 3 items:
1) A coordinate system in which one of its axes is parallel to the desired build direction (e.g. Z), 2) Select the proper additive manufacturing constraint (for example the ABZ manufacturing constraint ), and 3) Specify the minimum overhang angle needed (45 degrees in this case). These choices are selected in the Topology Region selection panel in Design Studio, as shown in Fig. 3.
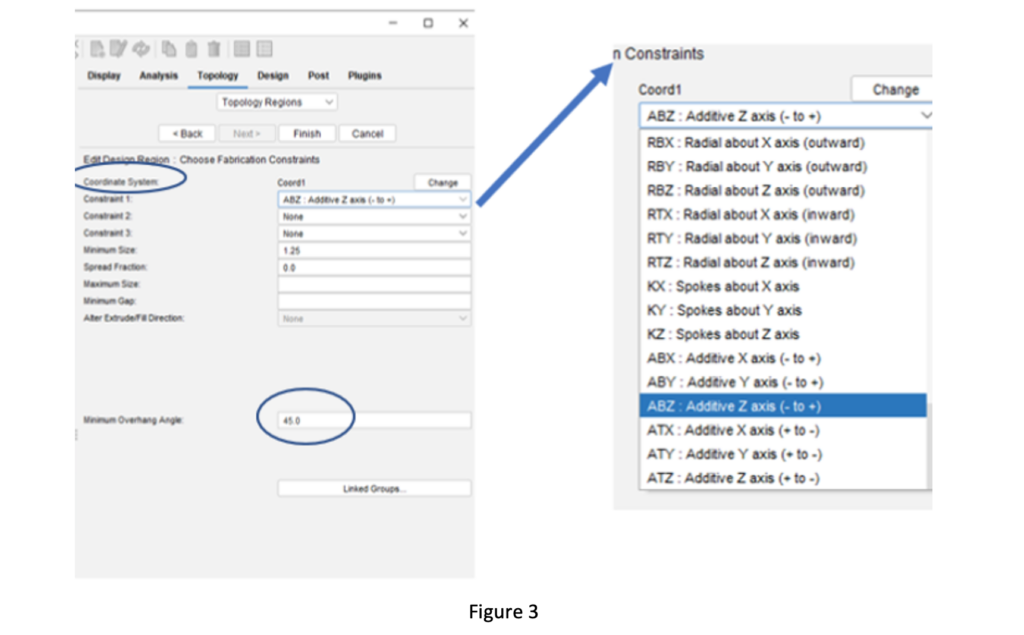
Topology Optimization with Overhang Constraint Results:
Figure 4 shows the final topology optimization results.
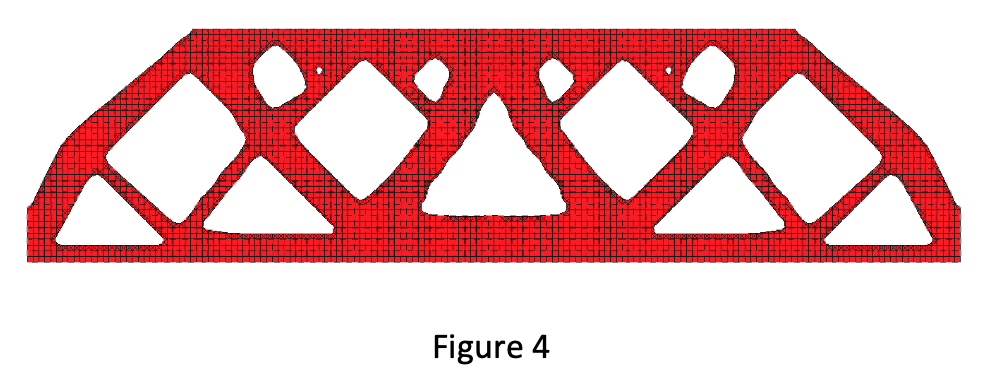
This answer can be printed using a 3D printer that uses the FFF process as it does have shallow members or members which angle with respect to the vertical direction are below 45 degrees.
Summary:
Requiring topology optimization to produce printable answers is easy and effective with the GENESIS software and its GUI Design Studio. For more information, check example TPDSG040 in the Design Studio Examples Manual and/or leave a comment below.