Simulating a powder dosing system in additive manufacturing with EDEM: material model calibration approach and results
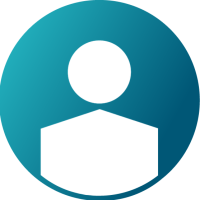
Additive manufacturing methods are rapidly growing in popularity across a wide range of industries including automotive, renewable energy and aerospace. The adoption of these methods is dictated by the need for precisely manufactured parts of increasing geometric complexity. In this context, the powder sintering method is an approach that has the potential to provide the required degree of precision and structural strength of finished products. These quality attributes, however, are determined by the interplay between the complex macro-mechanical behavior of the powder and the process operational parameters. Optimizing the manufacturing process therefore requires an in-depth understanding of the mechanics of the powder material and its response during the printing process. This is where EDEM simulation technology comes in. EDEM is a Discrete Element Method (DEM) software that simulates the behavior of granular materials in a range of industries, including powders processes. It can provide unparalleled insight into the fundamental micro and macro-mechanics of powder systems to inform equipment design and operation.
The strong need for understanding the fundamental mechanics of 3D printing systems motivated a collaboration between EDEM and The Barnes Group Advisors on the numerical modelling of a powder dosing system shown in Figure 1. This system is required to deliver a precise quantity of powder for subsequent spreading and its performance strongly affects the quality of the finished product. The major design challenge is ensuring a reliable and precise operation while processing powders of variable properties. Therefore, the focus of this work was on understanding the effect of the powder properties and wheel rotational velocity on the accuracy of dosing, in addition to the quality of the powder flow after dosing. To this end, EDEM material models for powders of two flowability extremes in the context of 3D printing were developed and used to simulate powder flow through the dosing wheel.
Figure 1. EDEM dosing wheel simulation model
MATERIAL MODEL CALIBRATION APPROACH
The EDEM material modelling requires optimization of the model input parameters using physical measurements as benchmarks. This step is necessary to ensure that the model approximates the behavior of the physical material well with respect to the phenomena of interest. A common approach is to optimize the model input parameters using measurements from a standard characterization test such as a shear cell or a rheometer as benchmarks. The Basic Flowability Energy (BFE) measurement of the FT4 powder rheometer was chosen as the physical response for optimization, because the measurement is conducted in a dynamic flow regime and a low stress state [1] corresponding to the expected conditions in the dosing wheel. The standard FT4 rheometer BFE test with a 50 ml vessel was modelled in EDEM. In the interest of computational efficiency only the test at the highest blade helical velocity of 100mm/s was simulated.
The powders were modeled using a meso-scopic modelling approach in order to insure practical computational time. In this approach, the macro-mechanical behavior of the material is captured using a particle size on an intermediate or mesoscale to achieve high computational efficiency [3]. Paired particles with an aspect ratio of 1.25 were used in order to capture the effects of particle non-sphericity on the bulk behavior of the material. The adopted meso-scopic modelling approach makes the use of the physical particle size distribution less meaningful, therefore the powder was modelled as a mono-dispersed system in the interest of simplicity. The EEPA contact model was used to model the virtual particle interaction in order to capture the complex elasto-plastic-adhesive behavior of powders. The conditioning cycle in the physical test was found to have a negligibly small effect on the computed BFE and was ignored in the interest of efficiency. The filling was modelled by the random rainfall method. The simulation stages are illustrated in Figure 2.
Figure 2. EDEM simulation of the FT4 rheometer basic flow energy test.
The input parameter optimization was conducted in a staged approach. A parameter sensitivity analysis was conducted first by the Design of Experiments (DoE) method. A set of twelve simulations were run in a Plackett-Burman configuration [2] and fitting a liner response model to the data. The response model was then used to assess the relative importance of the input parameters with respect to the responses of interest as well as to produce an initial estimate of the appropriate input parameter values. A further trial and error optimization was then conducted and a good agreement was achieved between the experimental and computed torque and flow energy responses as shown in Figures 3 and 4. The poured bulk density of the two powders was also closely matched by the model as shown in Table 1. The results were achieved with a relatively low number of simulations (18 in total) demonstrating the efficiency of the adopted calibration methodology. Users can refer to Pantaleev et al. 2017 [4] for further details.
Graph 1 & 2 – Measured and simulated torque on the impeller blade during the basic flow energy test cycle at 100mm/s blade tip speed.
Graph 3 & 4 – Measured and simulated basic flow energy at 100mm/s blade tip speed
Table 1. Measured and computed poured bulk density
Material | Physical bulk density (g/ml) | Simulated bulk density (g/ml) |
Powder 1 | 2.85 | 2.85 |
Powder 2 | 4.30 | 4.25 |
SIMULATION RESULTS AND ANALYSIS
The calibrated material models for the two powders of very different flowability were used to simulate the dosing process in order to understand the mechanics of the system and the effect of powder properties on it. The below video demonstrates some of the micromechanical level information available from the EDEM models such as particle compressive forces. In addition, useful macro-mechanical insight such as the prediction of flow rates and flow patterns after dosing can be obtained. This allows virtual prototyping to be conducted in EDEM to optimize the system leading to time and cost savings.
In conclusion, EDEM material models can capture the complex micromechanical behavior of powders and provide excellent quantitative predictions of complex physical responses after calibration. The efficient model calibration methodology adopted in this work requires only a small number of simulations, making the calibration of accurate models practical. The effect of powder properties on the mechanics of additive manufacturing processes can be studied with the resulting EDEM models. In addition, the models can be used to conduct virtual prototyping of equipment, resulting in cheaper and faster design optimization.
If you want to learn more about calibrating material models download our report: Calibrating DEM Models for Powder Simulation. This technical report discusses the latest challenges and advances in powder simulation, and provides guidelines for calibration.
References
[1] Freeman, R. (2007). Measuring the flow properties of consolidated, conditioned and aerated powders – A comparative study using a powder rheometer and a rotational shear cell. Powder Technology, 174(1–2), 25–33. https://doi.org/10.1016/j.powtec.2006.10.016
[2] R.L. Plackett and J.P. Burman (1946). The Design of Optimum Multifactorial Experiments. Biometrika 33 (4), 305–25. https://doi.org/10.1093%2Fbiomet%2F33.4.305
[3] Thakur, S. C., Morrissey, J. P., Sun, J., Chen, J. F., & Ooi, J. Y. (2014). Micromechanical analysis of cohesive granular materials using the discrete element method with an adhesive elasto-plastic contact model. Granular Matter, 16(3), 383–400. https://doi.org/10.1007/s10035-014-0506-4
[4] Pantaleev, S., Yordanova, S., Janda, A., Marigo, M., & Ooi, J. Y. (2017). An experimentally validated DEM study of powder mixing in a paddle blade mixer. Powder Technology, 311, 287–302. https://doi.org/10.1016/j.powtec.2016.12.053