Transverse Weld Simulation
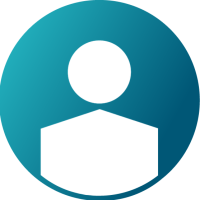

I have recently been using the Inspire Extrude Metals software to simulate the extrusion of Aluminum as well as a user-defined Plasticine material. The main focus of these simulations has been to observe the output transverse weld length.
The following trends that I have found in my simulation do not match my experimental data:
The simulation predicts that an increase in the extrusion ratio, in an otherwise identical die, results in a decrease of the weld length. The change in extrusion ratio caused an increase in exit velocity, which when changed to match the lower extrusion ratio example caused a further change in the weld length. The material I was using was strain-rate insensitive so the velocity should have no effect on the transverse weld.
Changing the material in the simulated model had no effect on the weld length.
I was curious if anyone knows the parameters that have an effect on the weld length within the Inspire Extrude Metals software. Are the results I am seeing expected, or is it possible that I am making mistakes in my model?