Application Of romAI for Stress and Load Prediction From Strains
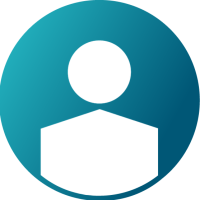

Introduction:
A digital twin is a computerized model of an object or a system that covers its entire lifecycle. It utilizes real-time data for constant updates, and integrates simulation, machine learning, and reasoning algorithms to support decision-making. Sensors are used on physical objects to gather data on crucial performance metrics like deformation, temperature etc. The data is used to update the computerized models, which are then used to run simulations. Simulations are used to detect performance issues, propose corrections, and provide enhancements to physical objects. While simulations are extensively used during the design phase, a digital twin becomes exceptionally useful when we have real-time data.
So, this makes the question: “How can one use simulation, digital twin and real-time data in combination to obtain insight into a real-world situation?” very relevant. This article tries to provide a very simple example of a bracket that uses Finite Element simulations (FEA) from OptiStruct, romAI module from Activate, and “simulated test data” to predict stress and loads from strain field.
The Problem:
Let us say a structure is available on which FEA can be run. This constitutes the simulation model. Stress and strain fields can be evaluated on this model; in simple words, stress and strains at various locations can be computed for any load that is applied on the structure. Now, let us say, a totally new strain field is provided – for e.g., a strain field from measurement on the physical part. Starting only from the information of strain in 2 locations:
- Can we use romAI to predict the stress in the bracket?
- Can we use romAI to predict the load that causes the 2 given strains?
The romAI model along with the FE model, constitutes the digital twin of the physical part. The romAI model utilizes simulations to build a real-time compliant “Reduced Order Model (ROM)” of the part; it then takes in the input from measurements, and then predicts the stress, and the load which would cause this strain field.
The Part:
The part is taken from this page: https://grabcad.com/library/ge-engine-bracket-10-1. It is used to demonstrate the methodology outlined in the last section.
Figure 1: FE model of the bracket
The Methodology:
Figure 2: Methodology
An FE model of the bracket is prepared. Appropriate material properties, loads, boundary conditions and output are defined.
Figure 3: FE model with loads and boundary conditions
To build the ROM, it is required that the strains and stresses for known loads are computed. The loads are assumed to act only in one quadrant as shown below. It is just a matter of expanding the load cases if this problem needs to be extended to other quadrants.
Figure 4: Assumed load directions.
It is to be noted that there is only one simulation – which contains multiple load steps. Static analysis is used to simulate the stress and strain for given loads.
Figure 5: Load steps used for romAI generation.
A ROM of the bracket is then built using romAI in Activate:
- Input: vonMises strains at accessible locations (2 locations)
- Output: vonMises stress at different critical locations (6 locations); Loads at pin (2 loads: Y and Z directions)
Figure 6: Locations where stresses and strains are obtained for ROM generation.
For each output, a separate ROM is generated in romAI.
The created ROMs (contained in a FMU block) are tested in Activate where new values of strain (in the 2 identified locations) are added as input to obtain stress values at the 6 locations and the loads in Y and Z direction.
Figure 7: FMU blocks used for stress at each location, and loads (Y and Z direction load)
For verifying that the romAI model is accurate, we use a “simulated test dataset”. This is done since we do not have test data available. We obtain a new strain field by running the FE model with random values of loads. We then obtain the strains from this and input it into the romAI model to obtain the stresses. These values of stresses from romAI are compared with stresses from FEA. The table below shows the comparison of results. The error values greater than 10% are colored in red.
(a)
(b)
Figure 8: Loads and stress comparison between romAI and FEA [(a) Y and Z direction loads (b) Stresses at 6 different locations]
Known limitations:
- It is assumed that the FE model is an exact computer replica of the part in service. Towards this end, for every such case, it is extremely important to ensure that the FE model is built accurately and tested for several cases of loads from the field. The accuracy of the romAI model depends entirely on this premise.
- Only static analysis is used in this simulation; nonlinear behavior would be dependent on load and the load path that is taken to reach the load. So, modeling nonlinearity would need a different strategy.
Conclusions:
- A romAI model can predict the stress and loads with a fair amount of accuracy on a component by just knowing the strains at 2 locations. It could now be deployed and used in real-time to process sensor data in an operational digital twin.
- The procedure can be extended to more complex structures and mechanisms:
- Determining the number of strain gauges on a component to completely characterize a structure.
- It can be extended to determine the loads at bolt locations given the strain at some points in a structure.
Comments
-
Hello Mr Dixit,
can you please provide the FE model and results? I would like to try the entire calculation process myself.
Best regards
0 -
Hello Mr.Melikov,
Thank you for your interest in this topic.
Can you please send your details to my email id: rajiv.dixit@altair.com? I can send you the link to the files.
Regards,
RajivD
0 -
Hello Mr. Melikov - Thanks again for reaching out. I have sent the the link to the files to your email id. Please let me know if you need any other details.
Regards,
RajivD
0