What it means to have "Flexible" joints in Inspire Motion
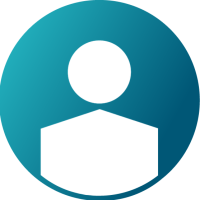

In Inspire Motion, joints can be treated as either “Rigid” or “Flexible”. By default, joints are Flexible, meaning they are modeled as Bushings. A Bushing element is a 6 DOF spring/damper connector that has stiffness and damping properties in each linear direction and about each axis, similar to the physical rubber bushings used largely in auto applications. Rigid joints, on the other hand are referred to as kinematic constraints where there is absolutely no compliance in the joints.
In Inspire Motion, by default, joints are stiff “Flexible” joints. They are called Flexible because they are Bushing elements, but they are stiff in the sense that the stiffness and damping values used are relatively high, essentially constraining certain DOF. The reason for using these stiff “Flexible” joints is so the user does not need to be concerned with redundant constraints, a common inherent behavior in rigid body modeling users typically try and avoid. Joints can be switched over to “Rigid” for purposes of defining joint friction or creating Couplers. However, in those cases the user should be familiar with redundant constraints and, depending on the goal of the simulation, if and how they should be avoided. Finally, flexible joint properties can be customized by the user to represent real-life bushing connectors.
Some additional notes on “Flexible” joints:
- Joints can be switched between Rigid and Flexible a) on a Global level through “Model Checking” section of the advanced Run Settings, or b) locally for each joint by using Property Editor.
Global setting:
Local setting:
- By default, “Flexible” joints are designed to behave as normal kinematic joints. The values used for the flexible joint stiffness and damping are automatically assumed by the software and are found under the advanced section of the Run Settings. They have been automatically determined based on details implicit to the model. You should not have to change the default values for the stiffness and damping.
- There is a “Sensor” for “Allowed Deformation” located under the advanced Run Settings. If the flexible joint deformation exceeds the “Allowable Deformation” specified, a warning will display. If the warning is triggered, either a) there is a conflict of motions or joints that needs to be addressed, or b) it was intentional because the user created a custom soft bushing that has large displacement. In case b, the sensor may optionally be turned off, since the deformation is expected.
- If desired, flexible joint properties can be customized so a joint behaves as a real-life flexible bushing. In this case, the joint State must be set to “Locked” and the joint Behavior set to “Flexible”. The properties can be changed (global level) through the advanced Run Settings or (local level) through the Property Editor for the specific joint. In this case, the large deformation warning may appear during the run and the sensor may optionally be turned off.