Spinning IPM motors with sensored FOC using real-time embedded software Altair Embed®
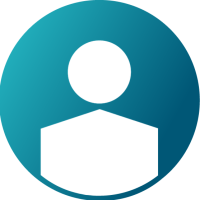
Spinning IPM motors with sensored FOC using real-time embedded software Embed®
Prof. Dr. Ir. Duco W. J. Pulle
Chief electrical drive consultant for Altair
Introduction
Interior Permanent Magnet machines known as (IPM) are characterized by a rotor that features buried rotor magnets, as shown in the topology below. They are closely tied to the PMsyn machine in terms of functionality and both use the same stator winding concept. However, moving magnets inside the rotor changes the inductance-rotor angle profile. For Pmsyn, the inductance is NOT a function of the rotor orientation. For IPM, stator inductance is a function of the rotor angle with two extreme cases defined by the d,q axis inductance values, as discussed in my video IPM theory.
The term called the salient inductance
, is typically less than zero (for many IPMs), which is why a negative is required to generate an equivalent flux
— shown in the IPM vector plot below — that supports the PM flux. This generates an additional reluctance torque component that boosts the torque/volume ratio of IPM machines and improves efficiency. IPMs are widely used for traction applications such as electrical vehicles. Control of IPMs is generally more complex due to the need control both direct and quadrature currents for a given reference torque value. Furthermore, magnetic saturation of the stator inductances
complicates the identification of the Max Torque per Amp (MTPA) function.
IPM topology IPM vector plot, case
To illustrate the function of the MTPA curve, it is helpful to rotate the current vector in the second quadrant (assuming flux-weakening IPM) by changing the angle . As the angle is increased, the electrodynamic shaft torque
reduces, while the synchronous reluctance shaft torque component
increases. Hence, there will be an optimum
value for a given
, that generates the highest shaft torque value. This leads to the function
, of which the inverse is use in combination with the current amplitude to determine the MTPA function
. (refer to Advanced Electrical Drives).
The process of determining the function is to connect the simulated or actual motor to a dynometer to maintain the shaft speed constant, typically at 25% of the rated shaft speed. Then set the current amplitude of the FOC sensored controller shown below and monitor the measured shaft torque as the angle
is varied. This process is repeated for a range of stator current steps
, as indicated below for the simulation model IPM_ISEA_phBv2T.vsm. During this process, the dynamometer (not shown below) is used to maintain the user-defined shaft speed.
MTPA figure
The function ,shown in the MTPA figure; is is generated using the salient controller algorithm (see our book AED), which determines the optimal angle
based on the user-defined reference input torque
value and the parameters
. Note that when using an experimental model, the inductance values will be prone to saturation, hence the salient controller parameters must be adapted. Alternatively, the practical
function can be derived directly from the measured (or simulated) results and then subsequently inverted to produce a function
that can be implemented using a lookup table when combined with the stator current steps used. This implies that for each
current step value (see MTPA figure), the direct and quadrature reference currents are calculated using:
,
Which leads to the MTPA plot for this machine, as shown below.
MTPA plot Embed MTPA module
Also shown in the figure above, the Embed MTPA module has, as input, the per unit reference shaft torque and as output, the two (per unit) reference values with parameters
as mentioned earlier. If the parameters match the real machine, then the generated reference currents match those shown in the MTPA plot.
The electrical drive shown below consists of the processor (MCU) that houses the control algorithms and all the functionality needed to use the measured current/voltages and generate the PWM signals for the converter. The currents, typically measured using in-line sensors (as opposed to shunts), are preferable to maximize the modulation index . Low-pass filters (LPF) are used to measure the converter output voltages and eliminate the PWM component. This implies that the average voltage per sample component remains and is not affected by converter dead-time or conductive voltage components of the semi-conductors. Hence, this gives the ability to accurately measure key motor parameters, provided that the LPF characteristics are taken into account, as is the case. Furthermore, access to phase voltages/currents is advantageous as the input power can also be found. The 12-bit ADC unit digitizes the incoming voltages/currents and these are sent to the Forward Clarke module that generates the motor current/voltages in
stationary coordinates, as shown in the vector plot above. These variables, together with the measured DC bus voltage, are required for the Controller and FOC data modules.
The purpose of the FOC Data module is to track the PM rotor flux vector and orientate the controller d-q synchronous coordinate system using an encoder input, as shown in the vector plot. This requires instantaneous knowledge of the flux speed
, angle
and PM flux amplitude.
Sensored IPM drive
The controller module consists of a synchronous current (see our book Applied Control of Electrical Drives) and speed controller, where use is made of the measured current vector and electrical shaft speed. In this case, the speed controller sets the reference torque, which can be used by a saliency controller (see our book AED) that sets the optimum reference
(that follows from the angle
) values (as mentioned above) based on the assumed PM flux and inductance values.
Application example
A simulation example of the AC drive mentioned above is shown below and consists of an 0.75 kW/3000 rpm Dietz H3-Typ PE DR 80-90/2 motor and a VESC6 MRK 3, 11-60V/80A controller.
VESC6 MKIII controller with ST link 0.75 kW IPM machine
The estimated motor parameters are:
This machine has a negative saliency term as commonly used. However, IPM machines with (known as flux-enhancement IPMs) are also emerging (for example Electric Vehicle Traction Motor - Equipmake), which need a different field-weakening strategy when compared to the classic field-weakening IPM (
) case.
The simulation example given below, shows an IRTF-based model of the machine connected to an FOC controller. The purpose of this simulation is to experimentally determine the shaft torque versus angle curves as shown in the MTPA curve plot above. In this case, the current vector amplitude must be selected prior to running the simulation. Then using the overplot feature, a set of amplitude current values can be deployed (and then rerunning the simulation) to arrive at the MTPA plot shown above. Such an approach can also be done experimentally for a given IPM attached to a dynometer (or a similar motor acting in PMsyn mode
) and using sensorless FOC with speed control.
Embed IPM simulation file
About the author
Prof. Dr. Ir. Duco W. J. Pulle
Forty years of experience in electrical drives, including 25 as a professor at various European Universities, including RWTH-ISEA, Germany, the world leader in electrical drives. Author/co-author of three books and numerous conference/journal papers.
Over the past fifteen years, I have been working as a consultant in the field of sensorless electrical drives with a wide range of machine types and power.
My vision and passion is to promote the use of real-time embedded control for electrical drive applications using Altair Embed. For this reason, a wide range of application examples has been developed that covers all machine types and control algorithms.
Educational background: Aviation College, B.Sc., M.Sc, Ph.D, flight engineer, and aviator.