Lattice filling options in Hyperworks
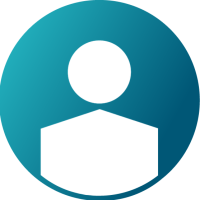

Three methods to fill a volume with lattice are illustrated in this document using examples.
Method1: This is the standard two-phase lattice optimization available in Optistruct, with a modification by the user to the solid load path at the end of Phase1 as explained later in the document. In Phase1, the design space is optimized as in a regular topology optimization, except that the intermediate density elements which lie between the user-defined density bounds are replaced by a lattice structure (1D beam/rod elements). Elements with density above the user-defined range are retained as solids and elements below the user-defined range are deleted. The lattice is considered as a load carrying member along with the solid part of the design. In Phase2, size optimization of the lattice beams is performed with additional constraints on stress, displacements etc. Euler buckling constraints are automatically considered for the lattice in Phase2.
Method2: A regular topology optimization is first performed on the design space using Optistruct, and the optimized design of the solid part is created based on the interpretation of the load path from topology optimization. The primary load path is the solid part. Any holes (voids) in the design can be filled with a lattice as explained later. If the lattice is added mainly for aesthetic appeal, then the lattice could be considered as a redundant structure as the solid part is already optimized for the given performance targets. In this case, size optimization of the lattice (like Phase2 above) need not be performed. There will of course be an increase in the overall mass and stiffness of the part due to the addition of the lattice. There is a trade-off between the increased mass and the increased aesthetic appeal due to the addition of the lattice.
Method2 is not limited to replacing holes/voids in an optimized design. This method in general can be used to replace any region of a solid structure with user-defined lattice, with an option of performing size optimization of the lattice. It is the responsibility of the user to make sure that the final design (solid + lattice) meets the performance targets.
Method3: Lattice is created using the lattice features available in the PolyMesh ribbon in Inspire. Any part of a structure can be replaced by unit cell lattice using one of the predetermined unit cell lattice types available in Inspire. No optimization of any kind is performed. Inspire version 2021 was used for the illustrative example in this document.
For any method, the viability of 3D printing should be assessed for the generated lattice. The process of blending the lattice to the solid part, creating a 3D mesh of the lattice to perform a detailed stress analysis, preparing the part with lattice for 3D printing etc. are not discussed in detail as they are beyond the technical scope of this document.
A brief overview of the three methods along with the flowchart of the workflow are given first, followed by the description of the steps involved for each method in the Appendix. This document should not be treated as a substitute for the solver manuals. The user should refer to the solver manuals for details of the concepts.