Investigation of Tablet Coating Processes Using Discrete Element Method Simulations
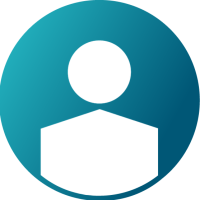
AUTHOR(S)
D. Suzzi, G. Toschkoff, J. G. Khinast, K. Knop, P. Kleinebudde, S. Just
PUBLISHER
American Institute of Chemical Engineers
SOURCE
AIChE Conference -2011 Annual Meeting
YEAR
ABSTRACT
In the pharmaceutical industry, drum coating is a widely used unit operation to produce tablet films of different purposes. In this process, a rotating drum accounts for the necessary mixing of the tablets, and a coating solution is injected from above by means of an atomizing nozzle. The applied coating layer(s) fulfill different functions, e.g. taste masking and coloring, control of the release of the active pharmaceutical ingredient (API) from the core of a tablet, application of an additional API, or protection of the tablet core from environmental influences.For all aspects of the coating mentioned above, the uniformity of coating is of great importance. This includes both, inter-tablet uniformity and intra-tablet uniformity. In fact, as inhomogeneity in the coating thickness can lead to serious hazards (e.g., significant variations in APIs delivery rate), a single tablet that fails testing can lead to the rejection of the whole batch.Although drum coating is a widespread technology in the pharmaceutical industry, process design is more often than not based on trial-and-error practices and operator experience. In recent years, parallel to an increased effort in experimental work, numerical simulations of particle motion using the Discrete Elements Method (DEM) have proven to be an important tool in the detailed investigation of the tablet coating process, as well as in other particle-based pharmaceutical processes.The aim of this work is to analyze and understand the effects of parameters like tablet form, fill volume or pan rotation speed on the intra-tablet coating variability [3] in different coating devices. To this end, DEM simulations are performed to numerically reproduce the tablet motion inside different coating machines. Material parameters needed for the simulation are gathered from measurements. For each geometry, different tablet shapes, namely bi-convex, oval and/or round, are modeled by the 'glued spheres' approach. Further parameter variations include different fill volumes or different rotational speeds.Important process attributes that one wants to know are, e.g., residence time of the tablets under the coating spray, intra-tablet coating variability, or tablets velocities pattern. While many of these quantities are fastidious or even impossible to get by experimentation, they are readily extracted from the DEM simulations results.
KEYWORDS
drum coating, pharmaceutical, Tablet coating