Defining Force data against varying pressure values for an AirSpring
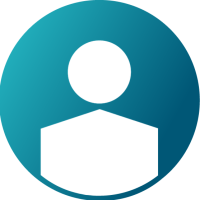

A frequent question that has been asked about AirSprings in MotionView. How is the force based off a pressure determined?
By looking over the .asg file (attached). The first column in the XY_DATA table contains spring heights at which measured or calculated forces are quoted in the second through last columns. In the example below, there are 6 columns - the first one is spring height. Each of the second through sixth columns correspond to force values at each of the pressures in the Z_DATA list, for each spring height.
The trim load corresponds to preload in a normal spring-damper entity, which should be calibrated to the observed corner weight minus unsprung mass.
Trim height is installed height of the spring at the "as-modeled" ride height of the suspension.
Together, these establish the baseline pressure - the table is then interpolated to find the corresponding force of the spring to maintain its height.
The PARAMETERS block is fed to an underlying geometric model.
Attached is an example model of the AirSpring with a displacement input to compress the spring by 15 mm.
Important Note: the air spring is only able to represent a rolling lobe airspring, the volume/pressure calculations will not be accurate enough for a convolute type spring, but we have a different solution for that. The simplest approach is a non-linear spring-damper but this only works for a single loading condition.