Container thermal stability is an important factor that influences the extrusion process and product quality. The temperature difference in billet could vary up to 150 °C. These large variations in temperature could influence material flow and product quality.
The non-uniform temperature at liner inner wall,
Heating Elements: Heating elements are placed inside the container and used for maintaining a proper temperature.
Feedback Control: Monitor temperature at thermocouples and regulate heating elements. These two features are used to determine the time required to reach thermal stability (periodic state)
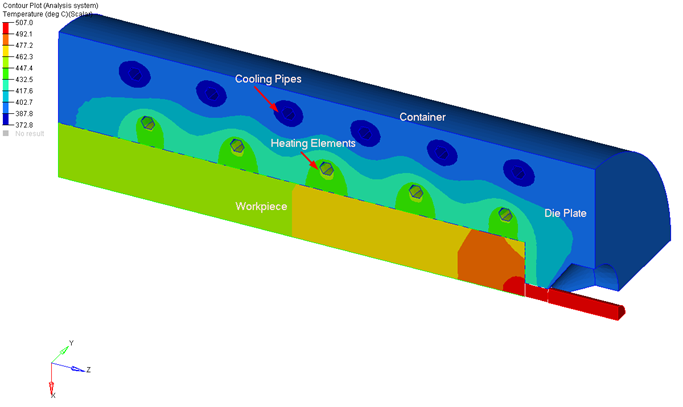
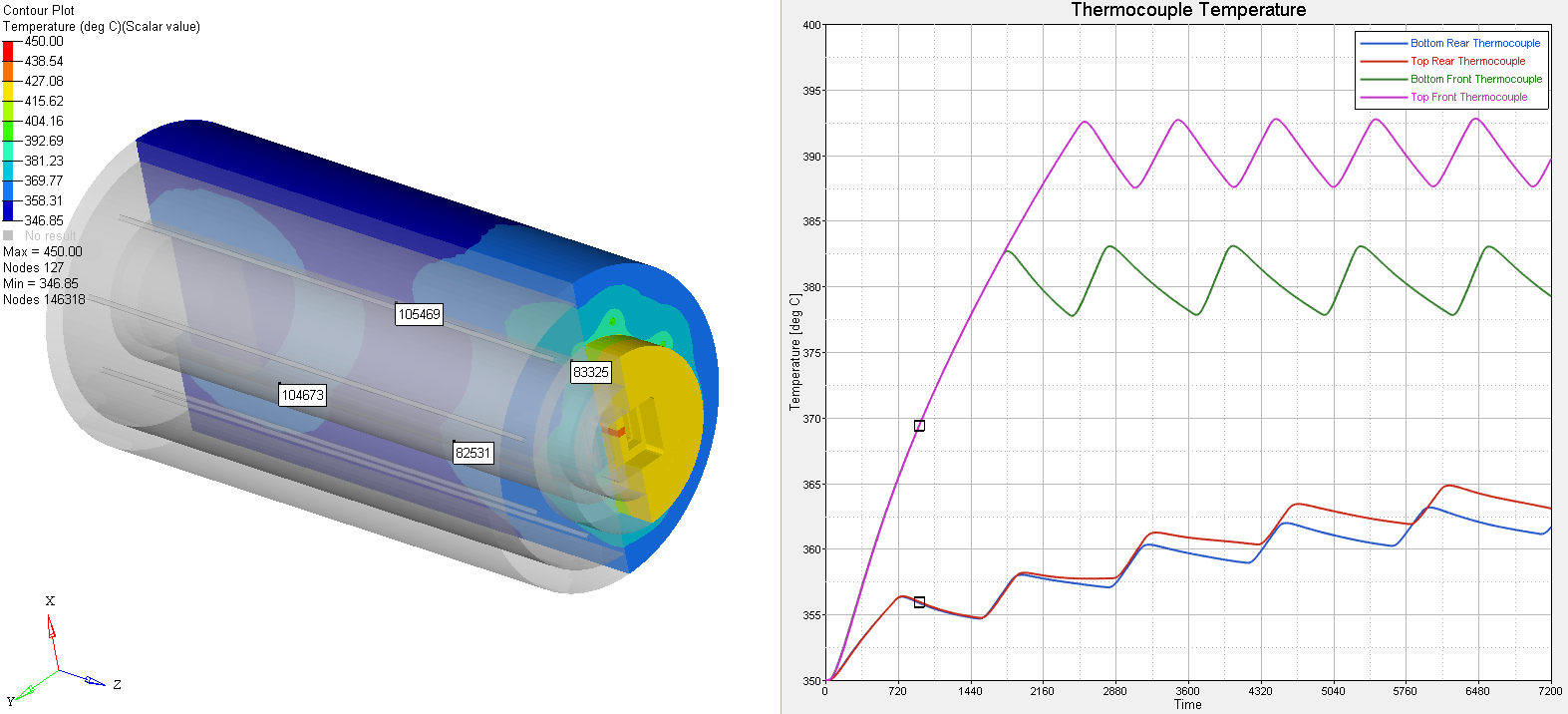
How to setup model:
- Setup model using Inspire Extrude as mentioned in Tutorial1 and have solver deck ready.
- Then create BCs for heating elements and add that information in solver deck. Lets say we want to define Heating element at location #1 as “HE1”
- Open GRF file and add heating element data block as shown below after MATASSIN END block.
BEGIN PROBLEMDATA HeatingElement HE1 { ThermocoupleName = "TC1" OnOffTemperature = 380 HeatFluxRampUpTime = 10 HeatFluxRampDownTime = 5 TemperatureTolerance = 1 } Thermocouple TC1 { Location = -0.536 182.18 -250.0 } END |
- ThermocoupleName : Specify the name of the thermocouple. This is defined in the next block
- OnOffTemperature : Specify the temperature at which the thermocouple should turn on and off. Here the value is 380 °C, which means this thermocouple will turn on when temperature falls below 380°C and turn off if the temperature goes above 380°C
- HeatFluxRampUpTime : Time needed to ram up the heating when the temperature falls below OnOffTemperature
- HeatFluxRampDownTime : Time needed to ram down the heating when the temperature goes above OnOffTemperature
- TemperatureTolerance : If tool temperature at a specified thermocouple location is within this tolerance then the thermocouple will active. This is to avoid numerical oscillation if temperatures is not exactly the same as OnOffTemperature.
- Location: X,Y, Z location of the thermocouple
- Now we will use this heating element information in one of BC as shown below,
ToolSurface TopFrontHE { IsHeatingElementPresent = "Yes" HeatingElementName = "HE1" X_Displacement = 0 Y_Displacement = 0 Z_Displacement = 0 HeatFlux = 7.5E4 #Material = Steel1010 } |
- IsHeatingElementPresent : Flag to specify is specific BC is heating elements of not
- HeatingElementName: Name of the heating element which has details about how it is going turn on and off
Save GRF fileRun simulationDuring simulation, the solver will write a .stat file containing temperature history at this thermocouple in "HeatingElementData.stat" file.You can also visualize results in HyperView